Hydrogen fuel cell technology in industry has received a lot of attention in recent years. Our study shows that the main factors affecting the cost of a hydrogen fuel cell system are shifted from battery pack performance and platinum (Pt) loading to the air supply subsystem. The air compressor, as the core device of the air supply subsystem of the hydrogen fuel cell, is driven by a motor to compress and humidify the filtered air and feed it into the hydrogen fuel cell reactor, where hydrogen and compress oxygen undergo an electrochemical reaction in the reactor, outputting electrical energy for use by external loads and its own air compressor.
However, 20% to 30% of the output power in the reactor is used for the air compressor, which accounts for about 80% of the overall power consumption of the hydrogen fuel cell system, which reduces the efficiency of the system and indirectly increases the cost of the hydrogen fuel cell system, which is not conducive to the wider application of hydrogen fuel cells in the industrial market.
Frequency inverter is also an accessory attached to the motor of the air compressor, and its advantages are: it can reduce the starting current of the air compressor through frequency conversion and reduce the impact on the hydrogen fuel cell system, and at the same time, it can automatically regulate the pressure so that the air compressor maintains a constant pressure operation, reduce the energy consumption of the system and prolong the service life of the equipment, so as to reduce the cost of the hydrogen fuel cell system. Figure 1 is the working diagram of the hydrogen fuel cell system.
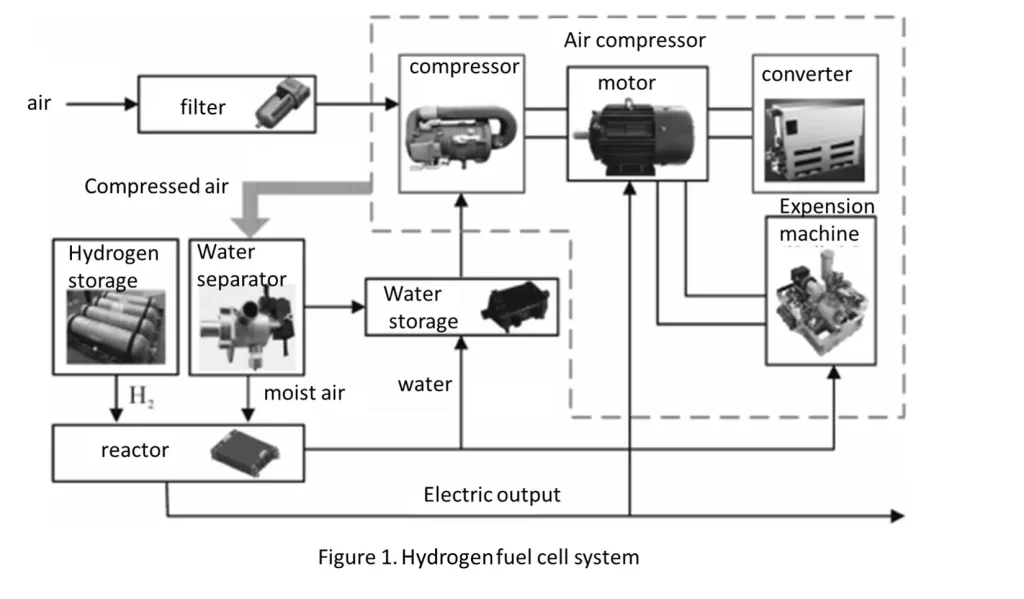
With the rapid development of the hydrogen fuel cell industry, the market for hydrogen fuel cell related parts and components is also promising.
1. Principle of air compressor frequency conversion technology
Frequency inverter is a device to control the hydrogen fuel cell air compressor through the principle of constant pressure air supply, so that the air compressor maintains a constant pressure output under the ideal pressure, thus achieving the effect of saving energy consumption. The following is a brief introduction to the advantages and principles of frequency inverter access in hydrogen fuel cell air compressors.
The change rule of hydrogen fuel cell system cost with air pressure, as shown in Figure2: with the increase of air supply pressure, the manufacturing cost of fuel cell can be effectively reduced; establishing the optimal air supply pressure of the air compressor has a good effect on the power consumption, the efficiency of the hydrogen fuel cell system and the cost of the improvement.
When the hydrogen fuel cell air compressor operates at 0.3MPa, keeping this pressure constant for air supply has a good effect on the improvement of system efficiency and cost reduction.
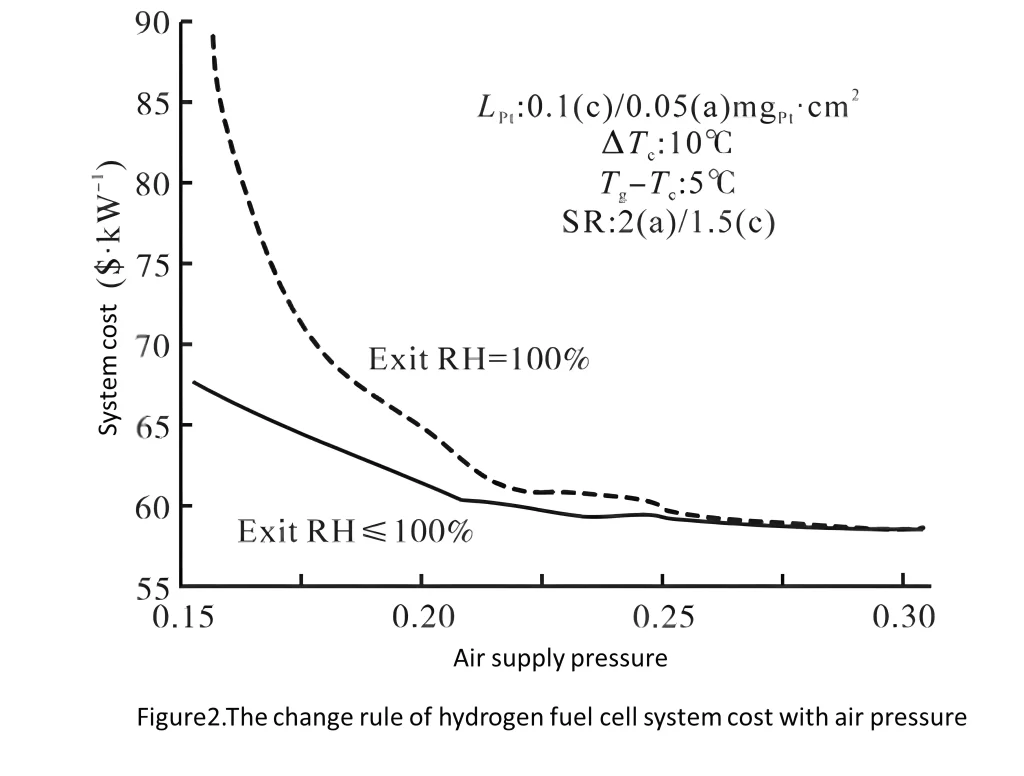
When the frequency inverter is connected to the air compressor in the hydrogen fuel cell, the motor speed can be further adjusted to keep the output pressure of the air compressor constant, and the inrush current during the startup of the hydrogen fuel cell can also be reduced to achieve the soft start of the motor in the air compressor of the hydrogen fuel cell and prolong the life of the equipment.
The solution has the following advantages: compared with the direct motor control without additional frequency inverter, the air compressor can achieve more stable air supply output; high versatility, according to the output power of the hydrogen fuel cell, adjust the appropriate air compressor output pressure, avoiding the cumbersome selection of air compressors for different output power of the hydrogen fuel cell; frequency inverter can be used with the expander to achieve a better energy-saving effect, reducing the air compressor output pressure, and improving the energy efficiency. The inverter can be used together with the expander to achieve better energy-saving effect, reduce the loss of the air compressor and improve the efficiency of the system.
The principle diagram of frequency conversion speed regulation is shown in Figure 3. The control process after the frequency inverter is connected is as follows: firstly, set the reference value of the output pressure of the air compressor, then compare it with the pressure value of the storage tank, obtain the corresponding frequency inverter through PID calculation, and then adjust the speed of the motor through the frequency inverter, and finally realise the constant pressure air supply.
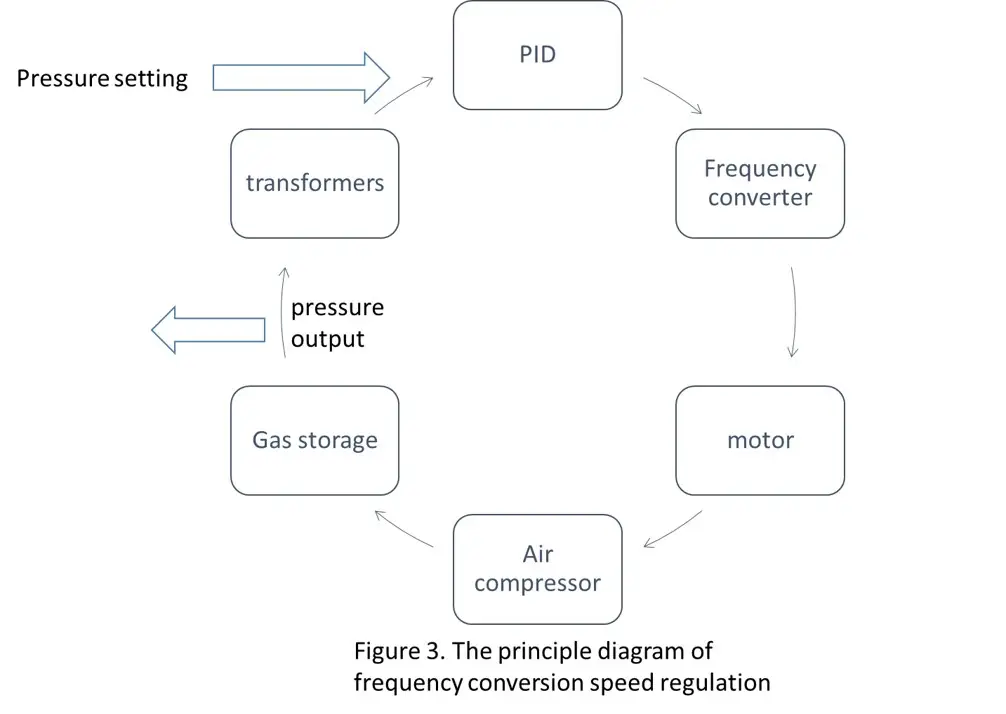
2. Current status of air compressor frequency inverter industry
2.1 Introduction of domestic and foreign manufacturers and products
1. INOVANCE
INOVANCE has several series of special frequency inverters for air compressors, all of which belong to low-voltage frequency inverters and are introduced as follows:
The output power range of CP200, CP300 and CP320 is 5.5~355kW, and the frequency 0~500Hz can be achieved;
CP650 series is a single frequency inverter integrated machine for air compressor application, which can output frequency 0~800Hz at 7.5~15kW output and 0~500Hz at 18.5~55kW output depending on the power range;
The CP700 product series adopts dual inverter and industrial frequency control, and can output a frequency range of 0 to 500Hz;
MD510 belongs to the special drive for high-speed motors, with a power range of 22~160kW and an output frequency of up to 1500Hz. it is worth noting that this product series adopts the PMVVC control developed by INOVANCE, which is suitable for synchronous motors and has relatively low parameter requirements for motors.
2. INVT
There are the following three models of Inventec’s frequency inverters for air compressors:
Goodrive300-01A series frequency inverter for air compressor is a product custom developed by INVISION for the application characteristics of the air compressor industry, which can be applied to the control of synchronous or asynchronous air compressors. The applicable motor capacity is 7.5-200kW, and the output frequency range is 0-400Hz;
Goodrive300-01A-RT series frequency inverter is a single frequency inverter all-in-one machine, applicable motor capacity is 7.5~37kW, output frequency range is 0~250Hz;
Goodrive300-21 series dual inverter all-in-one machine for air compressor is suitable for synchronous or asynchronous twin-screw air compressor, applicable motor capacity is 7.5~90kW, output frequency range is 0~400Hz.
3. V&T
V&T has V5-H-A9 frequency inverter for air compressors.
4. SINEE
Sine Electric’s A98E series is a permanent magnet screw air compressor special frequency inverter, with permanent magnet synchronous motor, the motor’s rated speed up to 60,000r/min.
5. Powtran Technology
PI500-C series frequency inverter for air compressor is designed for screw air compressor process, which can achieve better control of synchronous or asynchronous air compressor. It can be matched with permanent magnet synchronous motors, and the applicable motor capacity ranges from 7.5 to 400kW, the output frequency range is from 0 to 400Hz, the output frequency range is from 0 to 300Hz under vector control, and the output frequency range is from 0 to 3200Hz under V/f control.
6. EURA DRIVES
KY2000 series is a single frequency drive integrated machine for air compressors, which can provide single frequency drive for screw rod air compressors, and has been applied in Ingersoll Rand air compressors, and can be matched with permanent magnet synchronous motors.
7. FORIPOWER
Ultra-high-speed motor frequency controller products developed specifically for hydrogen fuel cell system air compressor motors, using SVC control, the output frequency can reach 0 to 3000Hz, and the maximum motor speed can reach 180,000r/min.
8. FULING ELECTRIC
New Fuling Electric has H200 model air compressor frequency inverter.
9. MICNO
TE300A series air compressor special frequency inverter, in the V / f control can reach the output frequency 0 ~ 3000Hz, in the SVC control can reach the output frequency 0 ~ 300Hz.
10. Japan YASKAWA
E1000 uses high-efficiency synchronous motors and is a special frequency inverter for compressors. The 200V model can be applied to motor capacities ranging from 0.7 to 110kW; the 400V model can be applied to motor capacities ranging from 0.75 to 630kW.
11. Siemens
Siemens has SINAMICS-G120XA model compressor load special products.
12. DANFOSS
Danfoss FC103 is a special product for compressors.
13. Schneider Electric
Schneider has AVT212 model compressor industry-specific frequency inverter.
Next to the above mentioned air compressor frequency inverter products operating voltage, output current, output power, output frequency and the use of control methods are summarised in Table 1.
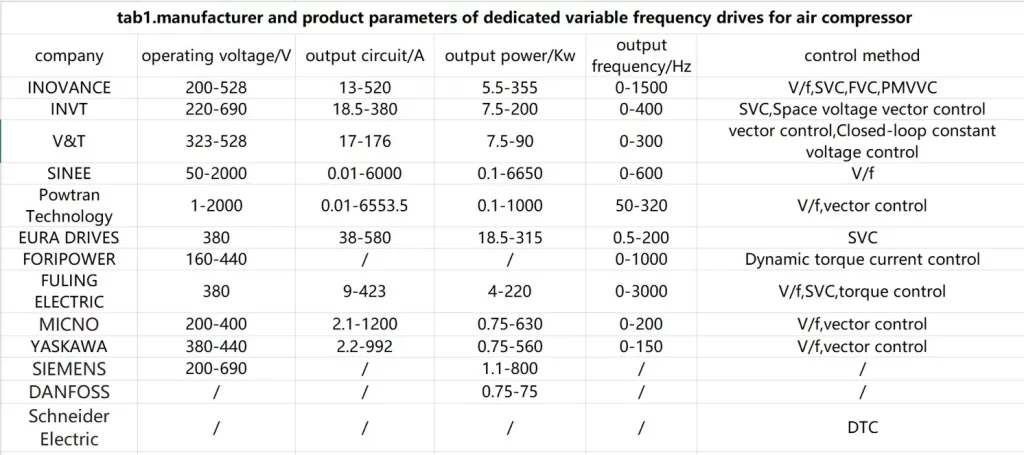
At present, most of the hydrogen fuel cell air compressor frequency inverters produced by manufacturers, most of their operating voltage between 200 and 690V, belonging to low-voltage frequency inverters; the output current of the frequency inverter is relatively high, and the output voltage of the product is generally the same as the input voltage, and the motor of the air compressor is working at a low voltage and high current.
The most commonly used control methods for air compressors for hydrogen fuel cells are speed sensorless vector control (also known as open-loop vector control (SVC)) and constant voltage and constant frequency control (V/f). By the products of Mackinaw and Putrans Technology, it can be seen that when V/f control is used, the output frequency can reach a very high frequency output, while under SVC and FVC (closed-loop vector control) control, the output frequency is generally in the range of a few hundred; although DTC control is also a commonly used control method of frequency inverters, only ABB adopts DTC control in the industrial products of frequency inverters dedicated to air compressors.
According to the above summary can be seen, Chinese manufacturers of air compressors special frequency inverter products in the indicators can replace foreign products, Chinese companies are developing rapidly.
2.2 Technical difficulties and development direction of air compressor frequency inverter
2.2.1 Frequency inverter application topology and control mode
The power range of portable auxiliary power supply is from 1W to 20kW, and the power range of hydrogen fuel cell vehicle field is from 1 to 300kW, both of which are adapted to medium and low voltage frequency inverters. The topology of the medium and low voltage frequency inverter is relatively uniform, all of them are two-level structure, as shown in Figure 4. The power range of hydrogen fuel cells in power plants and cogeneration applications can reach 0.5kW to 2MW, and high-voltage frequency inverters are required to drive them.
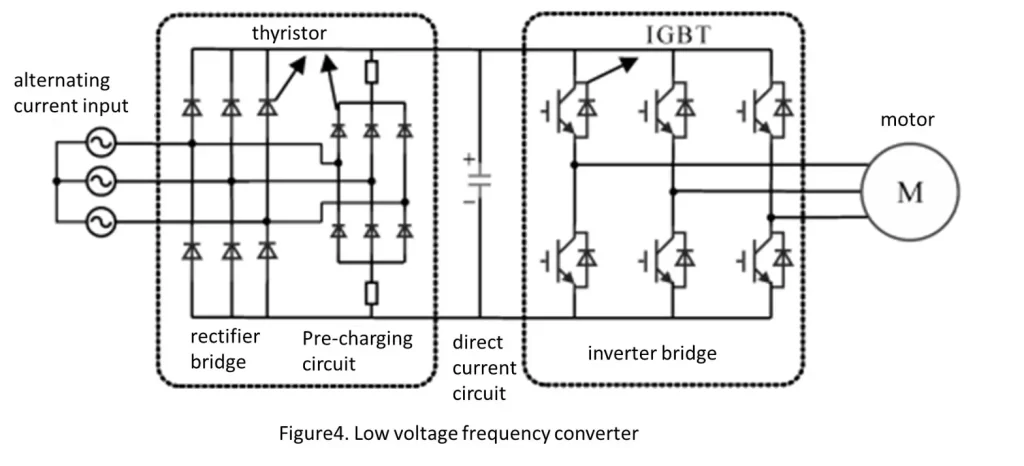
The two-level topology in Fig. 4 consists of three parts: rectifier, intermediate DC link and inverter. The rectifier part is an uncontrolled rectifier bridge circuit, the diode used in the device, and the function of the precharge loop is to suppress the impact of the starting current on the capacitor; the intermediate DC link is for filtering, DC energy storage and buffering reactive power; the inverter part is a fully-controlled device, the insulated gate bipolar transistor (IGBT), and the inverter topology achieves the two-level voltage output.
The commonly used control methods are V/f, FVC, SVC , and DTC. Their respective characteristics and application scenarios are described next.
The control algorithm of V/f is relatively simple, which controls the output torque of the motor, with the disadvantage of slow dynamic response and poor control accuracy, and can be used for loads with low control accuracy requirements, small load variations, and energy-saving requirements.
FVC control is to decompose the output current into excitation current and torque current to achieve separate control of torque and speed, with fast dynamic response. However, this control method requires sensors to identify motor parameters such as motor stator resistance and d, q-axis inductance, and is used for loads that require precise control and have high dynamic response capability.
SVC control mode is the same as FVC mode, but there is no sensor for feedback in the speed loop, the control accuracy is lower than FVC mode, and it needs online identification of rotor magnetic chain position angle and speed, which can be used for loads that need to control the torque and speed separately and do not have particularly high requirements for dynamic response and accuracy.
DTC control is to directly control the torque and flux of the motor without having to change between complex spatial coordinate systems, compared with vector control to simplify the controller structure, in the torque response and control accuracy has the advantage of being used for occasions that require high-performance control, especially in the large inertia load system that requires a fast transient torque response.
Technical difficulties, the core technology of frequency inverter includes power electronics and motor control algorithm two parts. At present, frequency inverters used in hydrogen fuel cell air compressors need to develop in the direction of high power density, high electromagnetic compatibility, high reliability, high versatility, high convergence and better fast synchronisation and other technologies.
In terms of power electronics, the hardware structures of low-voltage frequency inverters for hydrogen fuel cell air compressors in portable and transport applications are relatively mature, while the high-voltage frequency inverters for stationary power generation require the continuous development of new topologies.
2.2.2 High-speed motors
As the direct object of the frequency inverter to access the hydrogen fuel cell air compressor, the performance of the motor is critical to the entire hydrogen fuel cell system.
3. Conclusion
Hydrogen fuel cell air compressor is the core component of hydrogen fuel cell, in recent years, the industry has gradually adopted frequency inverter, with the advantages of reducing the energy consumption, extending the life of the system, which is conducive to reducing the cost of hydrogen fuel cell system, making the development more mature. Check new blog here.