Status and Prospect of Waste Heat Recovery and Reuse Technology in Packaging and Printing Industry
2024-03-11
Human activities and industrial production generate greenhouse gases, which contribute to global warming and other climate changes. The combustion of fossil fuels is the main source of greenhouse gas emissions. Therefore, one of the ways to reduce greenhouse gas emissions is to reduce the consumption of fossil fuels. However, in generating and utilizing energy, it is most effective to achieve minimization of energy loss and recovery of energy loss, which is always in the form of waste heat. There is a lot of heat production in industrial production, but the recycling efficiency is low because the heat is more dispersed and the recycling is limited, so the utilization of energy is low.
In order to reduce energy consumption and material consumption, improve resource utilization and comprehensive benefits, we can recycle and reuse the residual energy of waste heat, thus playing the role of resource recycling between the production system and the living system. To realize resource conservation and recycling, it is necessary to improve the production process and equipment, maximize the resources from the production chain through the whole life and recycle, so that the production and life cycle will be linked. For printing enterprises, if they want to develop a circular economy, commit to energy saving and emission reduction, and practice green printing, it is necessary to strengthen the recycling and reuse of waste heat and energy in the production process. Through the waste heat recovery device of the air compressor system, our company explains its application in different aspects such as power generation, refrigeration and heat storage.
1. Low Temperature Waste Heat Power Generation
1.1 Organic Rankine Cycle Power Generation
In thermodynamics, the Carnot cycle is described as the most likely effective thermal cycle due to the absence of heat loss, and it consists of four reversible processes, two isothermal and two adiabatic. It is equivalent to a cycle of reversible heat engine expansion and compression. Organic Rankine Cycle (ORC) technology is a solution to convert thermal energy into mechanical or electrical energy. It has been applied to the recovery of low and medium enthalpy heat streams (e.g., industrial waste heat, gas turbines and internal combustion engines) and renewable heat sources (solar, biomass, ocean or geothermal). During the cycle, organic materials with low boiling points are vaporized, and the gas absorbs heat and expands to do work to drive the generator.
The ORC unit equipment mainly consists of an evaporator, a condenser, a turbine-expander, a mass pump, and a generator, etc. The working principle of ORC is shown in Figure 1. The evaporator is one of the important components of the ORC system, and its main function is to transfer heat to the working fluid at a low temperature, causing a phase change. ORC systems offer many advantages over other widely used power generation technologies, but ORC conversion efficiencies can vary widely with system size: large, sophisticated plants can have electrical efficiencies as high as 25%, while small-scale and micro-ORC applications have electrical efficiencies of less than 10%.
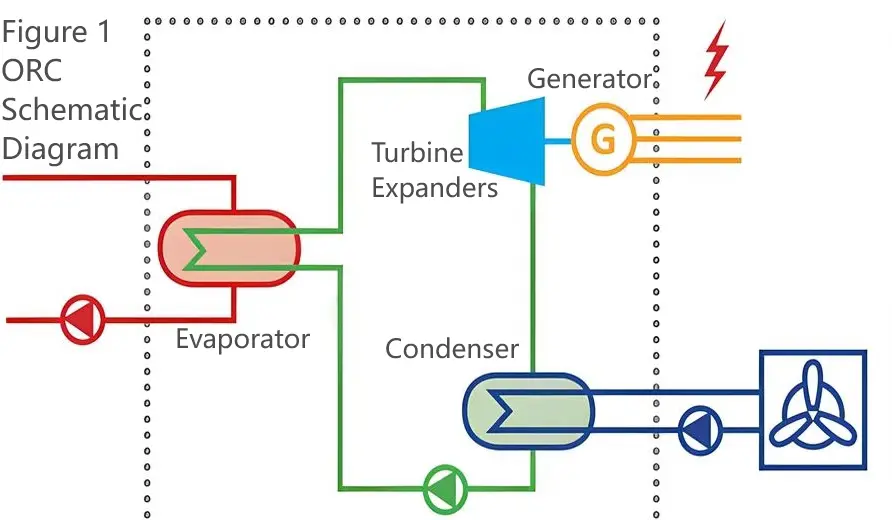
1.2 Kalina Cycle (KC)
In the 1980s, Kalina proposed a thermodynamic cycle with ammonia-water as the work material, which not only has a high thermoelectric efficiency, but is also suitable for low and moderate temperature heat sources and small power requirements. Ammonia is volatilized in the process of heating the mixed mass, the residual liquid concentration decreases, the saturated vapor pressure increases, and the system is more flexible than azeotropic evaporation. Characteristic of the first version of the Kalina cycle is that in an intermediate pressure, in a second condenser after the separator, additional degrees of freedom are allowed for the composition of the boiling mixture and the distillation unit is allowed to operate at a lower pressure than the maximum pressure. The significant efficiency benefits of the Kalina cycle are realized through heat collection in the evaporator and heat release in the condenser.
When the ammonia-water mixture is heated, the more volatile ammonia is more likely to evaporate first than pure water. As the concentration of ammonia in the residual fluid decreases, the saturation temperature gradually increases, which provides a better matched heat source for the hot gas. The working fluid is broken up into streams of different concentrations, which demonstrates great flexibility for optimized heat recovery and facilitates condensation at pressures higher than atmospheric pressure. Among different KC systems, KCS-11 (Kalina Cycle-11) is an effective method to utilize geothermal energy and has been recognized by many researchers. A scientist studied and compared the performance of ORC and KCS-11 used for low temperature geothermal heat sources.
They concluded that the KCS-11 performs better than the ORC under specific conditions such as moderate turbine inlet pressures. A researcher later proposed an improved Kalina cycle design for low-temperature geothermal power generation, which is a power cycle device that converts some of the waste heat from KCS-11 into electricity. The instability of industrial waste heat causes the KC to operate under non-design conditions, which results in errors in the design values of system performance. Adjusting the mass fraction of ammonia in KC can improve the average thermal efficiency, so the recovery of wasted low-temperature waste heat from industrial processes by this equipment can promote the recycling development of enterprises.
2. Low Temperature Waste Heat Refrigeration
Absorption refrigeration powered by low-temperature heat energy realizes the goal of two-tier cooling and heating without atmospheric pollution. Among the different waste heat recovery systems currently employed, absorption heat transfer is one of the most interesting energy saving devices, which consumes negligible primary energy. Such systems can raise the temperature of the waste heat to a higher temperature so that it can be recycled in industrial processes, avoiding environmental damage and mitigating climate change. In most cases, half of the heat provided by a heat source is available for use at a certain temperature, while the other half is discharged at a lower temperature. In addition, absorption heat transfer does not require high maintenance and operating costs.
The performance of absorption refrigeration systems is very dependent on the nature of the mass pair. Ammonia-water and water-lithium bromide are the commonly used mass pairs for heat transfer. Some of the undesirable properties of ammonia (i.e., toxicity, volatility, and flammability) and lithium bromide (i.e., corrosion or crystallization of lithium bromide at elevated temperatures or high levels of condensation) have compelled many researchers to dedicate themselves to the study of new work pairs to improve the performance of absorption systems. In addition, the limitations of the temperature of the heat source utilized by absorption refrigeration systems and the low energy efficiency have led researchers to continually attempt to improve the configurations of absorption refrigeration units, including advanced double-effect system configurations.
2.1 LiBr Absorption Refrigeration
LiBr refrigeration can borrow a lot of waste heat to recover secondary energy, including the evaporator, condenser, absorber, generator and other components. The performance of the absorber is generally enhanced by adjusting the vapor-liquid interface area of the absorber. In order to reduce the size of the absorber, a researcher used a fully conical nozzle for LiBr/water solution droplets. In order to optimize the vapor-liquid interfacial area and improve the system efficiency, a researcher installed an adiabatic absorber in a LiBr microsorption/absorption refrigeration system. In the LiBr cycle, adding new equipment can also improve the performance of the system. Absorption refrigeration systems have a higher coefficient of performance and higher elevated temperatures than single absorption refrigeration systems.
A researcher combined a single-effect absorption refrigeration system with an ejector and utilized the potential energy of the original airflow, which not only achieved the purpose of reducing energy consumption and improving system performance, but also reduced the manufacturing cost of the ejector device. A researcher has proposed a novel LiBr cycle that consists of an absorption cycle with an absorption generator and a heat exchanger, which can utilize 80-150 benefits of heat, and it can also be operated in both single- and double-effect modes. Most of the current research on the economics of LiBr absorption refrigeration systems is limited to the calculation and optimization of heat exchanger area. One researcher compared the performance of ORC and LiBr absorption refrigeration cycles. Absorption refrigeration cycle ORC using a non azeotropic workmass is more thermally economical than an ORC system using a pure workmass.
2.2 Waste Heat Ammonia Absorption Refrigerators
The ammonia absorption refrigeration cycle consists of two cycles: the refrigerant ammonia cycle and the absorption water cycle. NH3·H2O possesses good heat and mass transfer characteristics, but it is necessary to remove as much water vapor as possible from the ammonia refrigerant, otherwise it will result in a degradation of system performance. Some researchers have tried to add working medium pairs. Adding salt can overcome this drawback. The addition of LiBr facilitates the separation of ammonia molecules from the aqueous solution of the generator and helps to further improve the performance of the system, but it will hinder the absorption of NH3 molecules from the dilute solution.
A researcher proposed a new NH3-H2O-LiBr absorption cycle which utilizes an electrodialysis device to separate LiBr from the solution entering the absorber, leaving as much LiBr as possible in the generator. When the LiBr mass fraction is high, the separation of LiBr can reduce the operating temperature and substantially improve the performance of the ternary absorption cycle, thus increasing the heat absorption and cooling efficiency of the system. The study also demonstrated the feasibility and capability of the ammonia/salt absorption refrigeration cycle in cooling under air-cooled conditions. Thus, the advantage of this device is the simplicity of the cycle and it has great potential for the use of solar cooling or low-temperature heat sources. However, if the viscosity of the work medium used is high, it is not favorable for the heat and mass transfer process in the absorber and the generator.
3. Low Temperature Waste Heat Cold Storage
TES (Thermal Energy Storage) technology handles to some extent the problem of time inconsistency between the heat source and the heat user. Its storage is not limited by time. TES consists mainly of thermochemical heat storage, sensible heat storage and latent heat storage. Thermochemical thermal storage can store higher quality heat, but its system is cumbersome. The structure of this sensible heat storage system is relatively simple and widely used. The transfer process of latent heat storage is stable and the heat storage density is high. Meanwhile, the successful realization of TES depends on the long-term thermal stability and corrosion properties of phase change materials (PCM).
Phase change materials include organic (e.g. fatty acids, sugar alcohols) and inorganic (e.g. metals, salts and salt hydrates). Phase change materials should ensure that the phase change temperature remains within the operating temperature range of the system, and should have a high storage density and thermal conductivity. However, phase change materials have a low thermal conductivity, are highly unstable and are generally incompatible with container materials. TES can solve the problem of mismatch between heat demand and heat source in terms of distance and time. In order to utilize the waste heat that has not been processed so far, a researcher has proposed a mobile latent heat storage system with seawater as the energy storage material, and because of the great potential of this system, we can use the mobile latent heat storage system as a waste heat collector.
4. Waste Heat Recovery Carbon Neutral in Packaging and Printing Industry
Low-carbon economy, energy transition and green development are the positioning and objectives of future economic development and industrial upgrading. Packaging and printing industry is a major energy consumer, the recovery of waste heat in the process of product packaging and printing is one of the keys to energy-saving development of the relevant enterprises. To realize the green development of the economy, enterprises in packaging and printing should not only use environmentally friendly technology, but also start from the raw materials to improve, through the use of a number of new structures, new technologies, new materials, reduce the volume and cost, and at the same time do a good job of the same protection of the product.
In the packaging and printing enterprises, utilize the air end and cooler in the centralized centralized air supply room, and install the waste heat recovery device of the PM VSD screw air compressor between them ( Figure 2 ), so as to realize the efficient and environmentally friendly production and the development of circular economy in the printing enterprises.
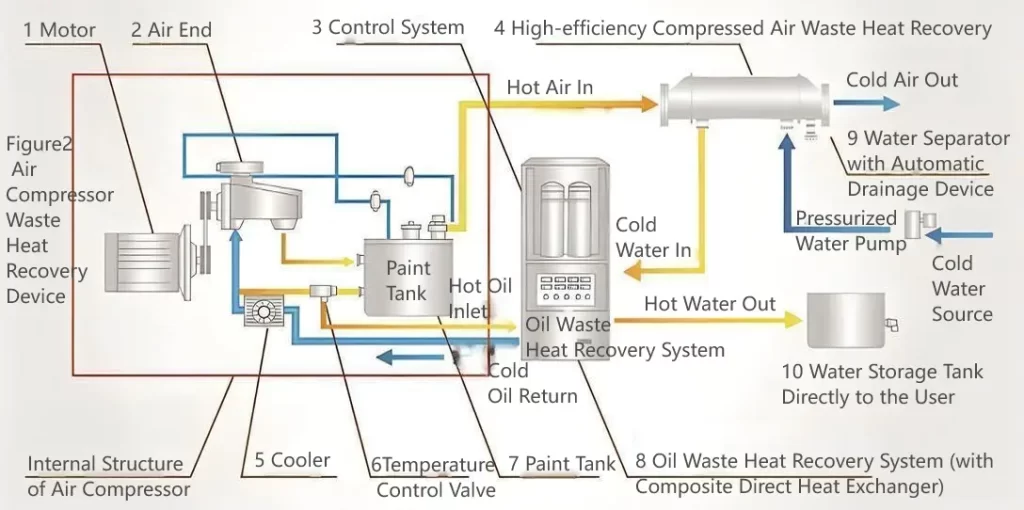
5. Conclusion
In the enterprises of printing and packaging, the printing plant will produce a large amount of waste heat in the production, the selection of appropriate heat transfer equipment and recovery program and the production process of waste heat recovery and reuse, can realize energy saving and emission reduction, and further guarantee the highly efficient and environmentally friendly production of the printing enterprises and the development of circular economy. In the centralized air supply room, install a unit of waste heat recovery of the screw air compressor between the air end and the cooler, allowing the waste heat recovery unit to exchange heat with the high-temperature lubricating oil of the air compressor.
While cooling down the high temperature lubricating oil, waste heat is recovered and processed in order to turn the cooling water used for power generation, cold storage, refrigeration and heating of hot water units into high-temperature hot water, thus realizing the recovery of waste heat from the air compressor. High-temperature hot water is stored centrally in the hot water storage tank, and then centrally rotated to the ink pre-heating device on the ink tank of the printing equipment, which provides a certain amount of hot water for circulation heating. In addition, the high-temperature hot water in the hot water storage tank is also used for staff bathroom water, cafeteria water, heating equipment and many other practical life.
In addition to solving the problems of high energy consumption of central air conditioning and unstable viscosity and fluidity of traditional rotary printing ink, the waste heat recovery technology also opens up the link between production and life, which reduces energy consumption and provides more stable hot water in a centralized manner, which is conducive to the realization of efficient and environmentally friendly production of printing enterprises and the development of circular economy. In conclusion, the technology of waste heat recovery and reuse can comprehensively and effectively recover waste heat, and it has great prospects for development.