Research on the Working Principle and Applicable Scenarios of Common Air Compressor
2024-04-07
With the current rapid economic development, Common Air Compressor is widely in demand, but there is more than one type of them. In order to prevent the improper purchase of equipment, the characteristics of the air compressor should be understanded in advance. The purpose of this article is to make the relevant personnel though a concise introduction to quickly understand the working principle of the air compressor, the most suitable working scenarios, in order to save the preparation time of the enterprises, less detour, reduce the operating costs of enterprises, improve economic efficiency.
1. Common Air Compressor working principle
1.1 Process flow of Air Compressor
The main equipment of the air compressor system includes air filters, air compressor sets, oil tanks, coolers and so on. The process flow is shown in Figure 1. At present, the most widely used is the centrifugal compressor. In this system, the air compressor workflow is shown in figure 1.
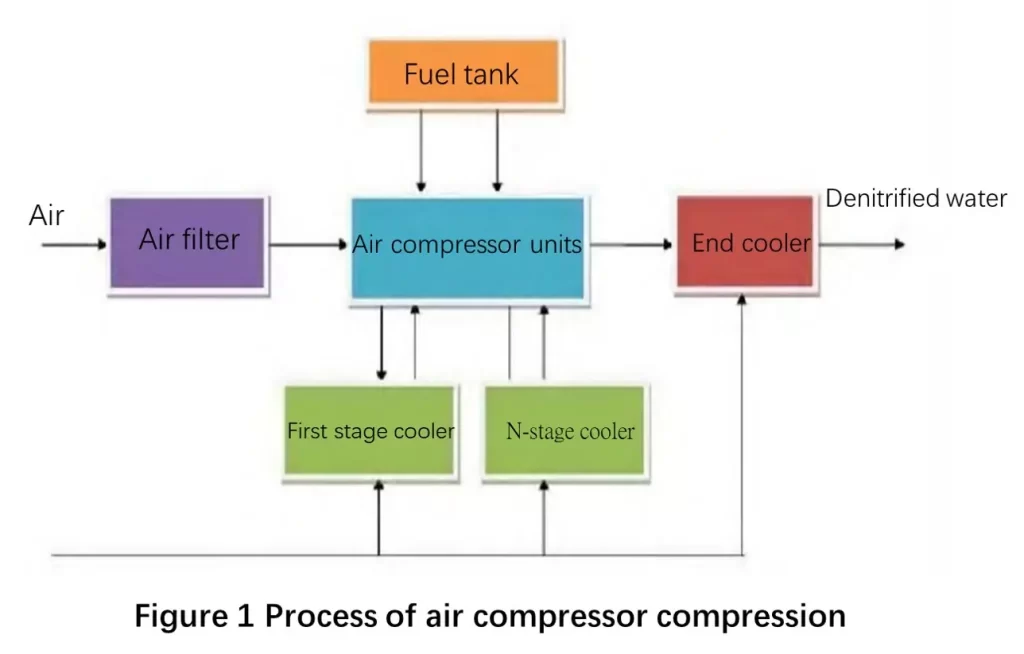
① Because there are particles, dust and other impurities in the air, which will damage the air compressor if they enter it, it has to pass through the filter first and reach the cleanliness requirement after filtration before entering the inside of the air compressor. After this treatment, the wear between the guide tube and the blade will not be aggravated by the entry of foreign matter, and the surface of the water cooler will not be contaminated by impurities, and the thermal conductivity will not be destroyed.
In air separation units, filters are generally of two types: wet and dry. In the actual operation process, the wet and dry filters are usually connected in series and then used. In this way, the filtration effect can be significantly improved. It should be noted that the wet filter in the front, dry filtration in the back, the effect is better.
② The clean air processed through the filter finally enters the compressor, the machine impeller will rotate at high speed, the air around the impeller is driven by it, then the velocity of the gas increases, the pressure increases, the impeller around the air is driven by it.
③ The high pressure gas after compression will then enter the diffuser, where the rate of the gas decreases and the pressure increases. The centrifugal compressor used in the air separation system usually uses multiple impellers, and the gas pressure is eventually increased to a predetermined value through the step-by-step compression of multiple impellers.
In the process of air compression, not only the pressure is increased, but also the temperature rises. This process will inevitably produce heat exchange with the outside world, part of the exchange process energy will be wasted, then the overall efficiency of the compressor will be pulled down. In order to solve this problem, we have introduced water cooler equipment. The water cooler is very effective in reducing the gas temperature, which is very helpful in improving the efficiency of the compressor. The role of lubricating oil is indispensable in the working process of the system, and the oil tank will always supply lubricant. After many compression processes, the air will eventually be sent to the nitrogen pre-cooler, where after cooling, it can be exported to the next device to use.
1.2 Air compressor system parameters and working principle
1.2.1 Common Air Compressor control method
In normal operation, the control part of the air compressor system mainly consists of 2 parts: Constant flow control/constant pressure control, air compressor start/stop control.
Constant flow control/constant pressure control: In normal operation, when the control system encounters fluctuations in the pressure or flow rate of the compressor, it stabilizes the pressure or flow rate at the outlet of the compressor. The measures taken are mainly: inlet and outlet flow adjustment, variable speed adjustment.
① Inlet flow adjustment is a common adjustment method used by the fixed speed centrifugal compressor, the operation of this way is relatively simple, the adjustment range is also wider, the cost is not too big.
② Variable speed regulation has the advantage of having the largest adjustment range and the lowest cost. The disadvantage is that it has a large uncertainty and is not suitable for demanding applications.
In specific application environments, the use of constant flow control or constant pressure control must be selected based on the operating conditions in which it is used, and selected to match the operating conditions. The primary objective of the control is the opening of the inlet guide vanes, which must be followed regardless of control method. The difference is that in constant flow control, the size of the pressure difference at the outlet of the compressor determines the opening of the inlet guide vane, but in constant pressure control, the outlet pressure of the compressor determines the opening of the inlet guide vane. In constant pressure control, the outlet pressure of the compressor determines the opening of the inlet guide vane. In large air separation systems, constant pressure control is usually chosen.
In the control part of the compressor working system, besides the above two main controls, there are other types of controls, such as the protection control when the compressor starts normally or when an accident occurs, the air compressor motor current overload protection control, and the automatic loading and unloading control. The existence of these controls adds help to the normal operation of the unit.
1.2.2 Common Air Compressor parameters
In the current market, the main performance of the air compressor is generally: exhaust pressure, flow, volume, working efficiency, working speed, power and so on. The details of these working parameters are as follows:
(1) Flow rate. Volumetric flow and mass flow are two commonly used methods of flow representation. In stationary compressors, the volume flow rate is more often used, and in mobile compressors, the mass flow rate is more often used. The flow capacity of a compressor is usually expressed in terms of the inlet volumetric flow in m3/min.
In the petroleum, chemical, air separation and other related industries, the volumetric flow rate (at standard conditions) is used in m3/h. Different compressors are used for different applications. Due to the varying size of the gas supply, it must be adjusted according to the process requirements in actual operation.
(2) Rotational speed. The unit of this parameter is r/min, which refers to the rotor rotation speed in the air compressor. The energy consumption of the compressor is greatly affected by the rotor speed.
(3) Outlet pressure. Usually, the outlet pressure refers to the exhaust pressure of the air compressor equipment. In the air separation system, the unit of this pressure is usually MPa.
Outlet pressure is a particularly important parameter in air compressors. The higher the required discharge pressure, the more it is for the selection of the equipment.
Parts of the equipment should be of high quality, strength and rigidity should meet certain requirements, so the purchase cost will also rise sharply.
(4) Power. The unit of this parameter is kW, and it refers to the power of the compressor.
(5) Efficiency. This parameter refers to the value of the effective power of the gas output of the compressor compared with the value of the power consumed by the compressor shaft.
On the nameplate of the compressor, the above parameters are clearly indicated. The working pressure, working temperature, relative humidity and other relevant parameters of the compressor are also indicated on the nameplate. The inlet conditions and gas medium are also indicated. The pressure at the outlet of the air compressor is an important parameter of the pressure control part of the system, and this parameter has a great influence on the efficiency and performance of the air compressor, and directly determines the performance of the air compressor outlet pressure control.
1.2.3 Air compressor working principle
The air compressor system process is generally a two-stage compression process in actual production, with a compression index between 1 and 1.5. Multi-stage air compressor for air compression, from a theoretical point of view, its exhaust temperature is very high. However, under normal circumstances, the final exhaust temperature of the machine shall not exceed the rated value, i.e., not more than 155℃-175℃, so, in the working process, the cooler will be used between the stages to reduce the temperature, and after the temperature is reduced, the gas can be sent to the next stage for further compression. The difference in outlet pressure between the two stages determines the compression temperature, which is proportional to the temperature, i.e. the larger the difference, the higher the temperature. Temperature in turn affects the volumetric efficiency of the compressor, therefore, the application of the intercooler in the process of the air compressor system is essential.
To summarize, using a multi-stage air compressor, starting from the first stage, the gas delivered to the higher stage is compressed step by step, and a cooling device is installed between the two stages to cool down the temperature, so as to avoid the flow of the gas with excessively high temperature to the next stage, in this way, the operating environment of the machine can be improved, and the specific volume of the gas can be reduced.
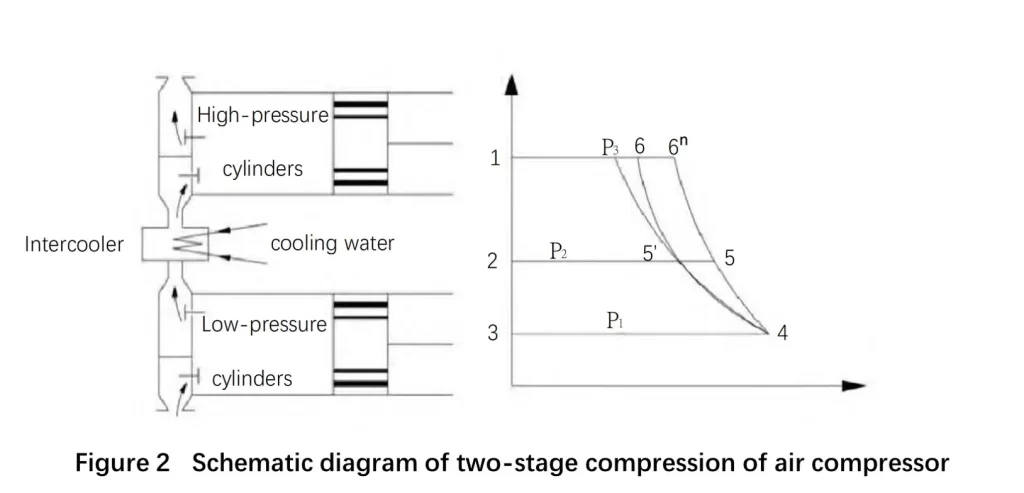
As shown in Fig. 2, the exhaust and suction processes are assumed to be under constant pressure control, and the graph is divided into three parts for detailed analysis. Curve 123455’61 is the first part, curve 123456”1 is the second part and 12345’P31 is the third part. The first part is the intermediate cooling process, which is the secondary compression of the air compressor. The second part is the single compression of the compressor. The third part is the constant temperature compression of the air compressor.
In the low-pressure suction process, the inlet valve of the low-pressure cylinder will be opened, at this time, the gas source is in a smooth and unchanged state, with the piston moving to the right, the volume of the gas is slowly getting bigger, and the low-pressure suction process is represented by the 3-4 line segments in Fig. 2.
In the process of low-pressure cylinder compression of gas, the inlet and outlet valves are closed. At this point, the piston moves to the left, the volume of the gas decreases, and the pressure increases. The compression of the gas in the low-pressure cylinder is shown in Fig. 2 by lines 4-5.
In the process of exhausting the low-pressure cylinder to the intercooler, the outlet valve is opened and the air pressure remains constant because the low-pressure cylinder has reached a predetermined pressure value. The volume of the gas slowly decreases with the venting action, which is represented by line 5-2 in Figure 2.
The cooling of the gas in the compressor-cooler is shown in 5-5′, where the pressure is also constant.
After neglecting the energy losses generated in the middle of the exhaust process of the intercooler and the suction process of the high-pressure cylinder, the two lines coincide and are represented by 2-5′ in Fig. 2.
In the case of an intermediate cooler, when the gas is compressed in the high-pressure cylinder, the inlet and outlet valves of the high-pressure cylinder are closed, and the state is similar to that of the low-pressure cylinder. When the piston moves to the left, the volume of the gas decreases and the pressure increases, which is indicated by 5-6′ in Fig. 2.
In the case of a cooler in the center, when the gas is discharged from the high-pressure cylinder, the outlet valve of the high-pressure cylinder is in the open state, and when the piston moves to the left, the pressure remains constant, and as the gas is discharged, its volume will slowly become smaller.
The advantages of using a multi-stage compression process in an air compressor, with devices such as heat exchangers for cooling between each stage, are as follows:
① The temperature of the final discharged gas is lower. This is because of the use of a first-stage compression.
In the case of one-stage compression, although the compressor cost is low and the structure is simple, the temperature of the gas discharged from the outlet is high, but after using the multi-stage compression process, and after the intermediate cooling process, the temperature of the final discharged gas product is appropriate.
②Lower energy consumption. From Figure 2, two-stage compression of air compressors can be deduced from the schematic diagram, if the compressor used compression method for single-stage compression, then the 123456”1 curve surrounded by the area that is the power it consumes. If the compressor is a two-stage compression method, the middle cooling method, then the sum of 23452 area and 125’61 area is the power consumed. The work consumed in isothermal compression is the area of 12345’P31. So isothermal compression consumes less work. Isothermal compression is only an ideal state, in practice, as long as the gas is compressed, heat is bound to be generated. Compressing and controlling to a constant temperature at the same time is difficult to achieve and too costly for practical production. Therefore, multi-stage compression, cooling in the middle of the way is the best way to achieve currently.
Figure 2 shows that the number of compressor stages is directly proportional to the number of intercoolers. After several compression and cooling processes, the more work is saved. In addition, the compression process will be changed to an infinite tendency to a constant temperature working state compression.
2. Classification of air compressor
Air compressor is a mechanical device, which, as a key component of the air separation plant, undertakes the task of compressing air and then delivering it to other equipment. Without the participation of the air compressor, the air separation equipment can not receive raw air, and without the air compressor, the refrigeration device and cooling equipment can not be used normally.
2.1 Classification according to use
In many fields of national economy, such as electric power, mining, chemical industry, refrigeration and other sectors, air compressors have long been widely used. Air compressor is the core equipment of high-pressure gas manufacturing, according to the use, it can be divided into the following four categories:
① Easy to transport: air compressor can compress the gas, making the gas easy to transport and save costs. After the treatment of air compressors, the gas is compressed into a high-pressure gas, the volume is greatly reduced, so that it can be loaded into containers for easy transportation, greatly saving transport space, very convenient.
② Used as force transmitting medium: gas can transmit quite a huge force to do work, so the air compressed by the air compressor can be used as a force transmitting medium, which is the transmission principle of air pressure.
③ Favorable for chemical reaction: Air compressor can provide compressed high-pressure gas source as experimental raw material for many chemical reactions. Because it can help some chemical reactions to be carried out better, the ions present in the gas can be better reorganized into molecules.
④ As an indispensable part of air separation equipment, air compressor is very important for air separation. In the air, the main components are nitrogen and oxygen. The content of oxygen is as high as 20%. In industrial oxygen production, it can be liquefied and separated by air separation system.
2.2 Classification by equipment type
In the air separation equipment, the most common air compressor has three types: Piston air compressor, turbine air compressor, screw air compressor.
2.2.1 Piston Air Compressor
Piston air compressors are used in environments where the flow rate is small but the required pressure is high. In the refrigeration industry, piston air compressors are widely used. In the process of use, the piston compressor motor operation will produce alternating current in the stator, alternating current will produce a magnetic field and drive the rotor to rotate. The rotor and the crankshaft adopt an interference fit. The crankshaft is driven by the rotor to rotate. Through the crankshaft connecting rod mechanism, the piston in the cylinder can realize reciprocating motion. After this series of actions, the gas in the cylinder is compressed, and finally the exhaust pressure of the compressor increases.
2.2.2 Turbine air compressor
Turbine air compressor are used in environments where the flow rate is high but the relative pressure requirement is not high. This type of model utilizes mechanical rotation in its operation. During the high-speed rotation of the impeller, centrifugal force is generated, under which the gas is sucked in from the center of the impeller, after which it moves along the channel between the blades and the blades, and finally flows to the edge of the impeller. The speed of the gas at the edge of the impeller is getting faster, and the gas pressure is also increasing, and at this time, it flows out at high speed in the gas channel, and after that, it enters into the diffuser channel, and the speed of the gas in this position becomes smaller, and the pressure becomes larger, and at this time, the kinetic energy will be transformed into the pressure energy. Finally, the gas coming out of the diffuser will enter the worm chamber output.
Turbine air compressor is also a common model, because of the nature, the movement of different structures, the model is also subdivided into two categories of axial air compressor, centrifugal air compressor.
① Axial flow air compressor has a large flow rate and high efficiency, but the disadvantage is easy to wear and consume more. During the working process of this model, the blades rotate at a high speed, and the axial inflow of gas is channeled into the guide vane for pressure expansion. The working range of this model is not large, because its exhaust pressure is not very stable, difficult to control. As a matter of fact, this type of compressor is generally less used, and unless there is a large consumer of compressed gas, this type of compressor will not be installed.
② Centrifugal air compressor produces good quality compressed air, which is suitable for most of the large air separation equipment on the market, so this type of air compressor is most widely used. Its impeller inlet pipe, worm chamber and other parts are important components. The air is diverted into the inlet pipe and gradually enters the impeller. The impeller is rotating at high speed in the working process, the rotation generates centrifugal force, and the gas is thrown out under the action of centrifugal force. The gas located at the edge of the impeller will increase in speed and then enter the worm shell. Inside the worm shell, the high-speed gas will be transformed into high pressure gas, which is finally discharged by the air compressor into the next stage.
2.2.3 Screw air compressors
Screw air compressors are used at the low-pressure level. The volume capacity is between that of a piston compressor and a turbine compressor. The PM VSD screw compressor is essentially a volumetric air compressor with the following main components: body, a pair of synchronizing gears, a master rotor, and a slave rotor (which can be meshed with each other). In the actual operation process, the meshing gears are continuously running, and the air is continuously being compressed and discharged, the whole process is uninterrupted and consistent, so the final output of compressed gas is also consistent.
3. Conclusion
In the industrial field, whether it is heavy industry or light industry, air compressors are widely used. There are three main types of air compressors on the market today, which are adapted to different working scenarios.
In summary, this paper describes and analyzes the process, parameters, and working principle of the air compressor one by one, pointing out the most suitable scene of different air compressor types, I hope that the relevant personnel to strengthen the understanding of the air compressor, the purchase and use of the air compessors. Read our new blog.