Precision Motor Control for Industrial Use: A Comprehensive Guide
In the modern industrial landscape, precision motor control plays a pivotal role in achieving optimal performance and efficiency. From automated assembly lines to industrial robotics, precision motor control systems are crucial for ensuring that machines operate at their highest potential. This article delves into the world of precision motor control for industrial use, explaining its importance, types, and applications, while optimizing for search engine visibility.
Understanding Precision Motor Control
Precision motor control refers to the techniques and technologies used to regulate the movement and operation of motors with great accuracy. Whether it’s a servo motor, stepper motor, or brushless DC motor (BLDC), the goal is to achieve high levels of precision in terms of speed, torque, and positioning. This control ensures smooth and efficient operations across a wide range of industries, including manufacturing, aerospace, and medical devices.
Motor control systems are responsible for directing the performance of these motors. At the core, there are two main types of motor control: open-loop and closed-loop systems. The closed-loop motor control system is more common in industrial use as it allows for feedback-based adjustments, ensuring the motor performs accurately according to the requirements.
W51 HD Three-Phase WEG Motor: The Best Precision Motor Control for Industrial Use
The W51 HD Three-Phase WEG Motor is engineered for high-demand industrial applications, making it a standout choice for precision motor control for industrial use. Known for its robust construction and energy-efficient design, the WEG W51 HD motor excels in challenging environments, offering reliability and minimal maintenance requirements. With a focus on high efficiency and durability, this motor is ideal for continuous-duty applications in sectors such as manufacturing, processing, and automation.
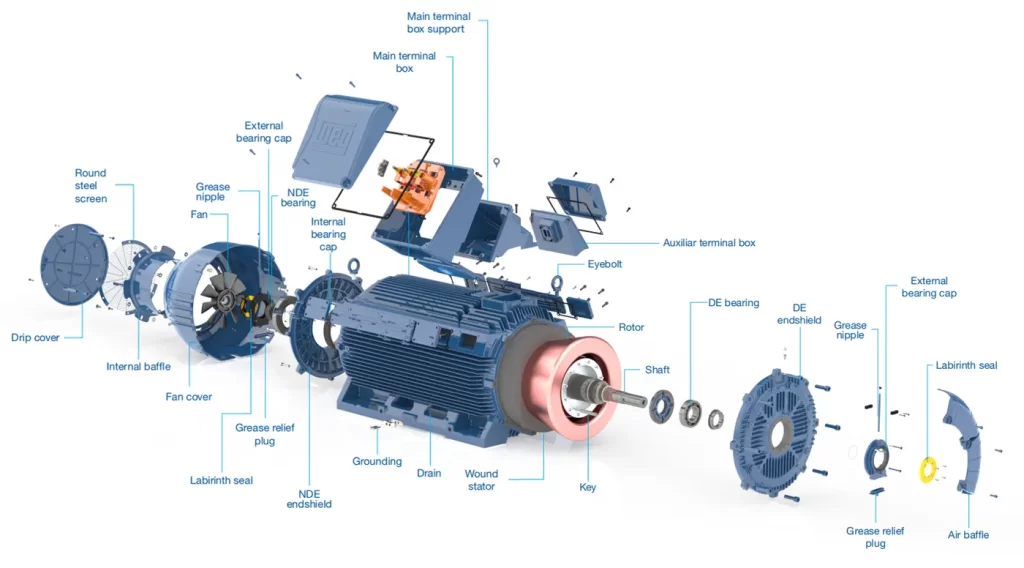
Key Features of the W51 HD Motor for Industrial Applications
Heavy-Duty Construction
Designed to endure tough industrial environments, the W51 HD Three-Phase WEG Motor is built for heavy-duty tasks. It can handle high working loads and operate over extended periods without compromising performance. Its durable construction ensures that it continues to operate at full capacity even in the most demanding conditions. This makes it perfect for industrial automation, processing plants, and manufacturing lines where equipment is subjected to heavy and continuous use.
High Efficiency
The W51 HD motor is built with energy efficiency in mind. It offers up to 10% energy savings, significantly reducing operational costs while maintaining high performance. This energy-efficient design is not only cost-effective but also contributes to sustainability by lowering carbon emissions. Its ability to operate with minimal energy consumption makes it a preferred choice for industries seeking to optimize their motor control systems.
Versatile Applications
The W51 HD Three-Phase WEG Motor is highly versatile, suitable for a wide range of industrial applications. It is commonly used in pumps, compressors, conveyors, and various types of large machinery. This motor is ideal for businesses in sectors such as textile manufacturing, material handling, and HVAC systems that require a reliable, energy-efficient power source to drive heavy equipment and machinery.
Advanced Cooling System
To maintain peak performance, the W51 HD motor is equipped with an advanced cooling system designed to prevent overheating. By keeping the motor within its optimal temperature range, the cooling system helps to maintain motor efficiency and extends the motor’s lifespan. This is particularly important for high-load applications where excessive heat can lead to motor failure and reduced operational efficiency.
Compact and Robust Design
Despite its powerful capabilities, the W51 HD motor boasts a compact design that makes it easier to install in confined spaces. Its high power density ensures that it delivers exceptional performance in a smaller footprint, allowing for greater flexibility in installation. Its robust construction makes it suitable for use in severe industrial conditions, offering reliability and longevity across various settings.
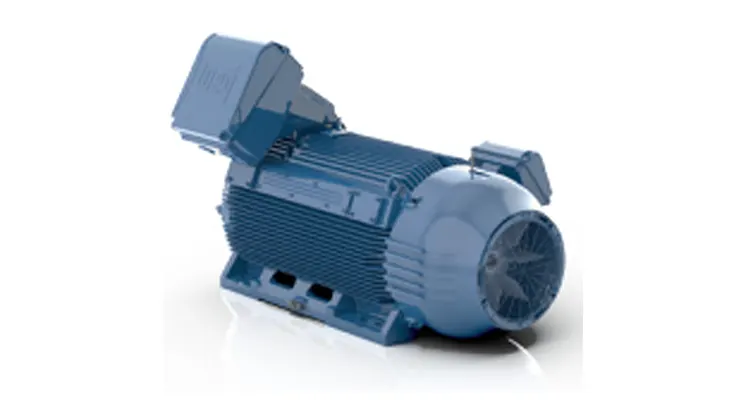
Maintenance and Precautions for the W51 HD Motor
To ensure long-lasting performance, regular maintenance of the W51 HD motor is essential. Key maintenance tasks include:
Regular inspections of bearings and electrical components.
Lubrication of bearings to reduce wear and tear.
Monitoring of the cooling system to ensure optimal temperature regulation.
Proper installation is also crucial. Mounting the motor as per the manufacturer’s instructions in a well-ventilated area will help prevent overheating and extend motor life. Moreover, it’s important to avoid overloading the motor by adhering to its rated capacity to prevent damage and overheating.
Advantages of Precision Motor Control for Industrial Use
1. Improved Accuracy and Repeatability
One of the primary benefits of high precision motor control is the ability to repeat actions with extreme accuracy. Whether it’s positioning a robotic arm or adjusting the speed of a conveyor belt, precision motor control ensures that the same action can be performed multiple times without deviation, essential for applications like medical devices and aerospace technologies.
2. Enhanced Energy Efficiency
By employing variable frequency drives (VFDs) and torque control, industrial systems can adjust motor speeds to match the load requirements. This helps reduce energy consumption and costs. Optimizing motor efficiency is vital in industries like material handling and manufacturing, where motors run for extended periods.
3. Reduced Vibration and Wear
Vibration in motors can cause significant damage over time. By using closed-loop control and feedback-based systems, industrial operations can minimize vibrations, extending the lifespan of equipment. Vibration reduction also improves the quality of manufactured products, particularly in aerospace and medical device manufacturing.
4. Increased System Integration
Motor control system integration allows different components of an industrial process to communicate seamlessly. By integrating PLC motor control systems and motion control algorithms, manufacturers can monitor and adjust motor functions in real-time, ensuring smoother operation and less downtime.
Conclusion
Precision motor control for industrial use is integral to the functioning of modern manufacturing systems. Whether it’s through servo motor control, stepper motor control, or variable frequency drive systems, precise motor control ensures that machinery operates with minimal errors, maximum efficiency, and enhanced reliability. For industries such as robotics, CNC machining, and automated packaging, these motor control systems are vital for maintaining high standards of productivity and quality.
At Vibmac, we specialize in providing top-tier motor control hardware and software solutions tailored to meet the needs of industrial applications. For more information on how precision motor control can benefit your operations, visit Vibmac Motor Control Solutions.