Application Analysis of Waste Heat Recovery of Air Compressor in Waste Incineration Power Station
2024-02-20
Oil-injected screw air compressor is widely used in various industries because of its stability and reliability, high efficiency, and low noise, low vibration. For waste incineration power station, the plant needs a large amount of compressed air, commonly used screw air compressor, but the screw air compressor in the air compression process produces a large amount of compression heat, through the direct cooling cooler, a large amount of heat dissipated in the air or by the cooling water away from the waste, not well utilized and wasted. With the improvement of people’s awareness of energy saving, more and more enterprises have realized that the recovery of compressed air compression heat can achieve the purpose of energy saving and emission reduction. Through the analysis of existing applications, the reasonable transformation of the air compressor unit can make reasonable use of this part of the energy and can improve the energy utilization efficiency of the whole plant.
For waste incineration power station, there are not many projects to carry out waste heat recovery of air compressor unit, with the world subsidies for biomass new energy projects gradually retreat, the need to improve the economic efficiency of the power plant is more urgent. Air compressor waste heat recovery, as an effective way to save energy, improve efficiency is gradually being emphasized, air compressor waste heat recovery has been widely proven to be available, efficient, in the waste incineration power plant application is also in the process of continuous exploration. Air compressor waste heat can not only be used to heat the staff shower water, but also can be used to heat the garbage pool in winter, and with the gradual increase of transformation and utilization projects, other feasible ways of application are also in the process of continuous experimentation.
1. Principle of Air Compressor and Energy Analysis: Waste Incineration Power Station
The screw air compressor generates compressed air through a pair of mutually meshing yin and yang rotors rotating in the cylinder, and its cycle can be divided into three processes: suction, and compression and exhaust. In the suction process, the yin and yang rotors rotate in opposite directions, the volume between the teeth expands, and the air is sucked into the cavity under the action of the internal vacuum; as the yin and yang rotors continue to rotate, the volume between the teeth starts to decrease due to the meshing of the rotor teeth, and the volume of the cavity decreases, resulting in higher pressure, thus realizing the compression of the air; with the further reduction of the volume between the teeth, the air with exhaust pressure is gradually discharged through the exhaust holes to the next level to repeat the same work, and the air is compressed continuously at multiple levels to achieve the required air pressure. Specific workflow is air compressor inhale the surrounding air through the air filter, so that it enters the air end, then continuously increase air pressure in the host, through the yin and yang rotor mesh movement, while spraying oil to lubricate and cool the screw constantly in the cavity. Air compressor produces high temperature and high pressure oil and gas mixture, most of the oil and gas mixture will be separated in the separator, the oil and gas will enter the respective cooling system, the air is discharged from the compressor after cooled, and then transported through the pipeline network to the final point of use, the high-temperature and high-pressure lubricating oil will return to the compressor for recycling after cooled.
Air compressor will produce a lot of heat in the process of compression of inhaled air, to ensure the stable operation of the compressor, this part of the heat needs to be taken away by the lubricating oil, and then the lubricating oil will be cooled through the internal heat exchanger, the heat exchange medium can be cooling water or air, so the air compressor can be divided into water-cooled compressors and air-cooled air compressors, in accordance with the cooling method. Air-cooled units generally use air ducts to export hot air out of the workshop, in the higher outdoor temperature environmental conditions, the cooling effect is not good, which will easily lead to high exhaust temperature of the compressor, affecting the stable operation; water-cooled units generally utilize the cooling water for cooling, the cooling water comes from outdoor cooling towers, and the circulating pump is used to supply the cooling water, the cooling towers and the circulating pumps need to consume electricity, so the electric load of the water-cooled units is generally higher. The stable operation of the cooling system of the air compressor unit directly affects the stable supply of compressed air, which is crucial for the smooth operation of the industrial system of the plant.
In the working process of the air compressor, only 15% of the energy is converted into high pressure air potential energy, and the remaining 85% is converted into heat energy through various ways, of which a small portion exists in the compressed air, and the vast majority exists in the lubricating oil. To make the lubricant recyclable, the lubricating oil is cooled by means of water cooling or air cooling. After calculation, this part of the heat accounts for about 75% of the total energy consumption of the air compressor, high temperature lubricating oil temperature can usually reach 80~100℃, energy quality is good, belongs to the unused high-quality energy of the power plant, can be completely reused.
2. Design and Analysis of Waste Incineration Power Station
For the utilization of waste heat from the air compressor of the waste incineration power station, the waste heat can be divided into two parts, one of which is used to heat the water for the shower of the employees in the plant; the other part is used to heat the garbage pool in winter to increase the temperature of the garbage pool and to promote the fermentation of the garbage.
2.1 Waste Heat Recovery for Shower
The system flow of waste heat recovery for shower supply is shown in Figure 1.
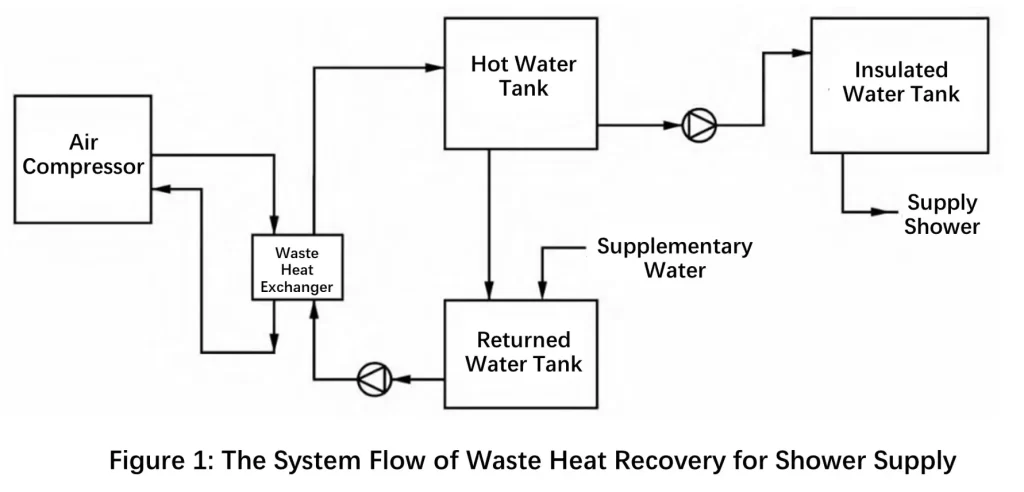
Waste incineration power stations generally have shower rooms in the main plant for off-duty bathing of employees, in addition, there are also corresponding shower facilities in the staff dormitory, in the past, we usually use electric heaters, if we can recover the waste heat from the compressor to supply the staff with showers, we can effectively save this part of the electrical energy.
Under the premise of not changing the original air compressor cooling system, the original high-temperature lubricant pipeline of the air compressor will be led out and connected to the oil circulating pipeline of the plate heat exchanger, in the plate heat exchanger, the high-temperature lubricant of the air compressor will be heat exchanged with the other side of the cooling water. One side of the heat exchanger cools the lubricating oil, and the other side of the heat exchanger heats the return water; the lubricating oil is connected back to the original piping system after heat exchange, and the cooling water provided takes away the heat of the high-temperature lubricating oil by the circulating pump, after which it is deposited into the hot-water tank, and hot water in the hot-water tank is delivered to the high-mounted insulated tank by the shower water supply pump, and it is necessary to set up a hot water supply line from the insulated tank to the showers for the use of the employees’ 24h showers.
The lubricating oil temperature of the air compressor can generally reach 80-100℃, and after passing through the plate heat exchanger, the cooling water can be heated up to 60-80℃, which can fully meet the employees’ shower demand. Polyurethane insulation is used for circulating hot water pipeline, and glass wool is used for each water tank for heat insulation, which can effectively reduce the intermediate heat loss.
Waste heat exchanger adopts plate heat exchanger W, this plate heat exchanger type is water-oil heat exchanger. Plate heat exchanger utilizes corrugated metal plates for heat transfer, which have precise structure and good heat transfer performance. Compared with other types of heat exchangers, plate heat exchanger is characterized by high heat transfer efficiency, wide range of installation scenarios, low price, applicable to a variety of heat transfer requirements, easy to replace and clean.
Adopting the external heat exchanger of plate heat exchanger has good flexibility and reliability because it does not change the original cooling system, and it can be quickly switched to the original system in case of waste heat exchanger failure, thus ensuring the normal operation of the air compressor.
2.2 Waste Heat Recovery with Waste Pool Heating
The system flow for waste heat recovery with waste pool heating is shown in Figure 2.
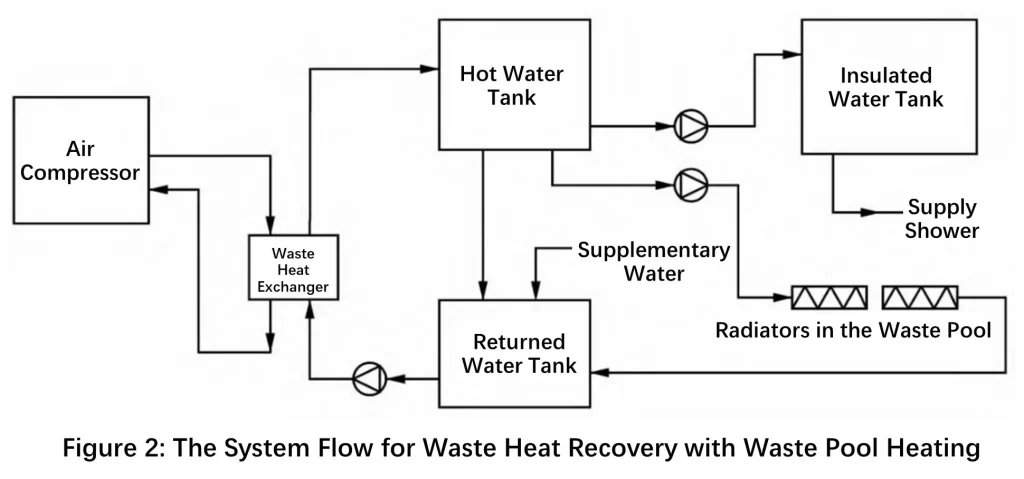
Waste incineration projects in the northern region generally have the problem of low temperature in the garbage pool in winter, and the garbage is not easy to burn. Generally, according to the fermentation cycle of garbage, the amount of garbage stored for 5-7d, the new garbage can be effectively fermented, and water can be analyzed out, and once the garbage is frozen, the water in the garbage can‘t be removed, which on the one hand, will reduce the calorific value of the garbage entering the furnace, and on the other hand, the garbage with too low a temperature is put into the incinerator, will further deteriorate the combustion condition of the garbage with a low calorific value. The primary fan of the incinerator keeps pumping out the gas in the garbage pool as the primary air, and the cold outdoor air keeps replenishing into the garbage pool, which makes the temperature of the garbage pool can never be increased. In winter in the northern region, when the temperature is lower than 10 ℃, the microbial activity in the garbage decreases, the fermentation is slow or even stops, the leachate cannot be precipitated, and the calorific value of the garbage is lower than the design value.
For frozen garbage, garbage moisture is solidified inside and outside the garbage, its melting needs heat and time, there is no arrangement of moisturizing facilities between the unloading hall and the garbage pit in the incineration power plant. People did not pay attention to the impact of garbage icing on incineration when designing the garbage pit, which makes the frozen garbage be put into the incinerator directly, the iced leachate, which accounts for 10% to 30% of the garbage volume, needs to absorb energy when melting, and the heat will be absorbed in the process of gasification in the furnace after icing melting, which increases the burden of operation of the grate under the same mechanical load of the grate so that the garbage can’t be burned adequately, and at the same time, it will also aggravate the work load of the flue gas purification system.
To address the problem of low winter temperature in the waste pool, the waste pool can be heated by the recovered waste heat, according to the calculation, the recovered heat is still surplus in addition to the application of staff showers. Set up radiators in the garbage pool, radiators using high efficiency finned stainless steel, not only to avoid the environment of the garbage pool on the corrosion of the radiators, but also to realize efficient heat transfer between the hot water and the air in the garbage pool.
As the air in the garbage pool is continuously pumped out by the primary fan, the air flows continuously, which can promote the heat exchange between the air and the radiator. Water is taken from the hot water tank and transported to the radiator in the garbage pool via the water supply pump, and then heat exchanged between the radiator in the garbage pool and the air in the garbage pool, which can increase the temperature of the garbage pool, thus avoiding the garbage from freezing, promoting the fermentation of garbage, and improving the calorific value of the garbage. The low-temperature water is returned to the return tank after heat exchange, and then sent to the residual heat exchanger for recycling through the circulating water pump. The return tank is equipped with an automatic replenishment function, so that the circulating water can be replenished quickly when the water level of the system is low.
2.3 System Control
This system can be programmed by PLC (Programmable Logic Controller) for automatic control, and the corresponding control program can be set according to different working conditions, according to the set temperature of oil, water and water level in the tank, associated with the start and stop of the corresponding pumps, which can meet the demand for automatic operation under different working conditions.
When the starting lubricant temperature of the air compressor reaches the set temperature, the circulating water pump of the waste heat exchanger will be opened automatically, and the waste heat recovery system will start to work. If the temperature of the oil returning from the waste heat exchanger exceeds the set temperature during the operation, the inlet valve of the original oil cooler of the air compressor will be opened to utilize its own cooling system to cool down the oil and make sure that the oil temperature will meet the requirements; the heat preservation tank is interlocked with its water supply pump and the water pump will be opened automatically to supply hot water when the water level drops. When the water level of the holding tank reaches the set height, the pump will be stopped automatically, which can realize the chain control of the water level of the tank and the water pump to keep the water level of the holding tank to meet the usage requirements. Refuse pool cooling pipeline pump is opened in winter conditions, hot water flows through the radiator set in the refuse pool, after heat exchange with the air, the return water enters into the return tank, the water level of the return tank falls to the set value, automatically open the water supply, the hot water tank water level rises to the limit automatically overflow to the return tank, the hot water tank is set to protect the water level, stop the external water supply in the case of a low water level, to prevent the pump from idling. This system is flexible in control and can be operated automatically according to the external conditions, which is safe and reliable.
3. Economic Benefit Analysis
Take a 2×350t/d waste incineration power station in the northern region as an example, there are 2 sets of water-cooled screw air compressors in continuous operation in this power station, with a rated exhaust volume of 21m3/min, a rated exhaust pressure of 0.8MPa, and a rated electric power of 132kW. According to the rated conditions of the compressor, the heat taken away by the lubricating oil accounts for 75% of the total energy consumption, and the heat exchanging efficiency of the waste heat recovery system is 70%, and the compressors run continuously every day for 300 days a year. If the heat exchanged is fully recovered and utilized, the total recovered heat Q=2×132×75%×70%×24×300×3600kJ=3.59×109kJ, which is equivalent to the amount of standard coal M=3.59×109÷29307÷1000=122.5t.
The waste incineration power station has 90 employees, according to each person showers once a day, each person rated water 80L, the average temperature of domestic water 15 ℃, the design of the water temperature of 60 ℃, the use of electric heating to produce hot water per day, the power consumption P=90×80×(60-15)×4.187÷3600=378kW·h. According to the price of electricity 0.8RMB/kW·h for 300 days one year, and the annual electricity cost N= 378×0.8×300=9.07×104 RMB and the annual electricity cost of shower can be saved by using this system is 9.07×104 RMB. The initial construction cost of this air compressor waste heat recovery system is about 2.4×105 RMB, and the annual operating cost N1 is the electricity cost of the pump, i.e., N1=1.5×3×20×300×0.8=2.16×104 RMB, and it can be concluded that the payback period of this system is about 3.5 year[24÷ (9.07-2.16)=3.5], and the system’s operating life is generally 15 year, and the life period is expected to Saving 1.0×106 yuan of electricity costs, so the economic benefits of this waste heat recovery system is obvious. Air compressor using waste heat recovery system for lubricating oil cooling, accordingly, reduce the air compressor on the plant’s industrial cooling water consumption, not only reduces the electric load of the water pump and mechanical ventilation cooling tower, reducing the plant’s electricity consumption, but also reduces the plant’s industrial water consumption, reduces the plant’s water costs, and improves the plant’s economic efficiency.
4 Concluding Remarks
Waste heat recovery is an important initiative for industrial enterprises to save energy and reduce consumption, our company focuses on waste heat recovery and utilization of air compressors in waste incineration power stations, briefly describes the working principle of the air compressor and the composition of the heat, discusses the waste heat recovery of air compressors in two different application paths, and analyzes the recovery system design and control mode. For the air compressor unit, the application of waste heat recovery system increases the external cooling path of the lubricating oil, so that the cooling system does not rely solely on the internal cooler, which improves the reliability of the cooling system, can further reduce the cooling temperature of the compressor lubricating oil, improve the efficiency of the air compressor unit, and increase the air compressor production under the same power consumption, which is also a good economic benefit from the point of view of the air compressor. From the above calculation and analysis, the lubricant waste heat of screw air compressor has good recycling conditions. For waste incineration power station, the waste heat recovery system of air compressor can not only be applied to the heating of the staff shower water, but also to the heating of garbage pool in winter, to increase the air temperature of garbage pool, which can promote the fermentation of garbage and increase the calorific value of garbage in the incinerator; it has been proved in practice that the system can make the incinerator burn steadily and increase the steam production, which can increase the power generation. It has been proved that the system can stabilize the combustion of incinerator, increase the steam production, and then increase the power generation, which has good economic benefits. The air compressor waste heat recovery system is simple to remodel, flexible and reliable in operation, with a short payback period. Click here to read blog.