Application Analysis of Permanent Magnet Frequency Conversion Screw Air Compressor in Medicine Manufacturing Enterprises
2024-02-23
Pharmaceutical industry W is currently one of the important international industries, with the rapid development of the modern pharmaceutical industry, people gradually pay more attention to the quality of drugs, modern automatic production line are more dependent on compressed air, for ensuring the quality of products, the quality of air is crucial. Air compressor is currently the most widely used air compression equipment, but in the process of using the air compressor has the problem of high-power consumption and high energy consumption, according to relevant statistics, the power consumption of air compressors accounts for about 15% of the power consumption of large-scale industrial equipment, high energy consumption of air compressors, serious secondary pollution and other inherent problems have been restricting its development. So, the measures to effectively reduce the energy consumption of air compressors is now a common international concern. Since 2008, permanent magnet frequency conversion air compressors have been favored for their green, durable, and low noise characteristics. Therefore, our company takes a pharmaceutical enterprise as the research object to study the application of permanent magnet frequency conversion air compressor.
1. Permanent magnet frequency conversion screw air compressor technology
1.1 Screw air compressor working principle
The working principle of screw air compre ssor includes four processes: suction, sealing and transportation, compression, and exhaust. When the screw rotates in the shell, the screw and the shell of the tooth groove meshes with each other, the air is sucked in by the air port, at the same time, the oil is also sucked in, due to the rotation of the tooth groove meshing surface, the oil and gas is sealed and transported to the exhaust port.; in the process of conveying the tooth groove meshing gap gradually becomes smaller, the oil and gas is compressed; when the tooth groove meshing surface rotates to the exhaust port, the oil and gas mixture of the higher pressure discharged from the machine body. Then it is discharged into the oil-air separator and after compression here, the discharged gas oil mixture undergoes collision, interception, turning and centrifugal separation., most of the oil medium will be separated from the air, and then contains a small amount of lubricating oil compressed air into the oil fine separator for the second separation, finally we can get a very low oil content of the compressed air. When the pressure of the air reaches the specified pressure value, if the minimum pressure valve is opened, the compressed air is discharged into the cooler for cooling and finally fed into the system for use. The screw air compressor adopts frequency converter to change the exhaust volume by changing the rotational speed of the screw rotor, so as to achieve the constant exhaust pressure and achieve the purpose of energy saving.
1.2 Principle of frequency conversion regulation
Frequency conversion screw air compressor is usually in constant torque operation, it adjust the speed of the motor through frequency conversion technology and according to the actual change of air supply, and always maintain a proportional relationship between the electrical output power and speed. The pressure at the exhaust port rises as the amount of air used decreases, and the air compressor controls the motor speed by providing feedback to the inverter to reduce the motor’s output. The pressure at the exhaust port rises as the air consumption decreases. The air compressor provides feedback to the inverter through a closed-loop system to control the motor speed and reduce the output power of the motor. And after the gas consumption rises, the pressure at the exhaust port will drop accordingly, at this time the frequency control system controls the motor speed to increase, and the output power of the motor will increase accordingly. Therefore, the frequency conversion air compressor can dynamically track the real-time load of the air supply system, and adaptively adjust the motor speed according to the tracking results, always keeping the pressure of the exhaust port at a constant state, thus making the operation of the air compressor more economical.
1.3 Frequency conversion control process
The frequency conversion speed control system is responsible for regulating the output pressure of the air compressor in compressed air state, while the frequency conversion speed control is based on the frequency converter. The pressure sensor, PLC, motor and other components form a constant pressure closed-loop control. Its working pressure can be set by the operation desk. The sensor recognizes the pressure value and then converts it into a current of 4~20 mA, and then the frequency converter compares and operates by PID to adjust the output frequency, to keep the speed of the motor within a suitable range. The results show that by adjusting the speed of the motor, the axial output power of the motor can be adjusted to make its air supply capacity compatible with the air consumption, which can achieve the effect of constant pressure air supply and power saving.
1.4 Permanent magnet frequency conversion technology
The permanent magnet frequency conversion air compressor adopts a spiral rotor, which utilizes power transmission to compress the rotor so that it encounters oil during operation, thus reducing friction loss. Therefore, the permanent magnet frequency conversion air compressor can also play the role of sealing, cooling, and lubrication in the process of contacting with oil, thus improving the performance of the equipment, increasing the efficiency of compression, and expanding the working range. The spiral rotor is the key component of the permanent magnet frequency conversion air compressor, which is driven by a permanent magnet motor with motor efficiency up to IE4 and protection level up to IP66, and it also equips with frequency conversion speed regulation, which enables the compressor to realize variable speed operation when subjected to local loads to achieve the purpose of high efficiency compression. The equipment adopts the direct traditional system, which has the advantages of simple control and good dynamics and is suitable for frequent starting or variable speed operation. In contrast, permanent magnet variable frequency motor requires higher temperature resistance and protection level, if the motor protection level is not high enough, dust can easily get inside the motor, accelerating winding failure and entering the bearing lubrication system, accelerating bearing wear. Therefore, under the adoption of high-efficiency permanent magnet frequency conversion motor, it is also necessary to pay attention to its motor protection level.
- Permanent magnet frequency conversion motor. Permanent magnet motors are regulated compared to constant speed motors, so the permanent magnet frequency conversion motor can improve the compression efficiency of the system through the regulating effect. Practical data shows that the permanent magnet frequency conversion motor improves the efficiency by up to 3%, fixed-speed motors and the aging of the equipment itself are the main factors in the unit’s performance deterioration. The permanent magnet frequency conversion motor has the function of frequency conversion adjustment, which avoids the influence of fixed speed performance decline. And the adjustment range is large. Permanent magnet frequency conversion air compressor has a large frequency adjustment range, it can be adjusted steplessly from 20% load to full load, and it operates more efficiently.
- Screw rotor. The screw rotor of the air compressor adopts 4+6 teeth program, the diameters of Yin and Yang rotors are equal, both have good rigidity, and the rigidity is close to equal, so it is not easy to be deformed. Besides, the loss of internal leakage is small, which is the standard number of teeth of the modern screw. The conventional scheme is the use of 5 + 6 teeth program, the diameter of the negative rotor is smaller than the positive rotor, and its stiffness is also poorer and less efficient.
- Small volume. Permanent magnet frequency conversion air compressor has a compact design, which is lighter and easier to carry than the traditional air compressor. Secondly, the speed of its compressor can be adjusted by frequency conversion.
- Low noise. The vibration of permanent magnet frequency conversion air compressor is relatively small, so you won’t hear the obvious noise, even under full load condition, it only emits 75dB noise.
- Durable. Since the magnetic levitation cooler has no lubrication system, there is no need for related maintenance and repair, so the service life and reliability of the system are greatly improved.
2. Technical Background of Energy Saving Retrofit in a Pharmaceutical Company
At the end of 2003, the air compression system of a pharmaceutical enterprise complex was formally put into production, and it has been 15 years since then, and the on-site test shows that the system is in good working condition and can work normally; however, due to the large attenuation of the air volume of the air compressor, most of the equipments are already obsolete, and it is difficult to purchase many parts and components, which results in that the equipments can’t be maintained in time, and they can’t be used normally, so it will have a certain impact on the air quality of the production workshop, which can no longer guarantee the production environment. Field tests show that some compressed air mainframes have a high level of volume attenuation, and the COP is lower than 3.5, the overall compressed air system of the air volume decreased by 12%, resulting in a large energy consumption of the system and producing a large amount of energy waste.
3. Overview of the original permanent magnet frequency conversion air compressor for pharmaceutical companies
The compressed air system of the production workshop of a pharmaceutical company complex consists of two 35.1kW compressed air main engines and one 22kW compressed air main engine, mainly for the complex production workshop to provide air to ensure that the quality of compressed air production workshop in line with GMP requirements. The fixed-speed compression system is equipped with only one post-treatment dryer and four sets of filters, and there is only one air outlet in the main pipeline.
4. Remodeling program design
To save system operating costs and improve the quality of compressed air, our company, after researching and comprehensively evaluating the compressed air systems sold on the market, plans to replace the original air compressors of the complex building with 2 sets of permanent magnet frequency conversion air compressors. In accordance with the principle that a single unit can meet the entire gas supply and have a margin, our company replaces the corresponding supporting facilities to achieve the purpose of one with a reserve, which not only improves air quality, but also avoids the need to add compressed air machines because of adding air-using equipment at a later stage.
4.1 Project Construction Objectives
The main objectives are to improve the system COP, the quality of compressed air and the safety performance of the air supply equipment, so that we can ensure that the quality of compressed air in the plant meets the GMP standard and we are able to reduce the energy consumption of the compressed air system.
4.2 Main contents of project construction
Dismantle the original No.1 and No.2 air compressors and the corresponding refrigerating dryers, filters, distribution cabinets and machine room pipelines, and install two sets of permanent magnet frequency conversion air compressors with air supply capacity of 2.45-12.32m³/min (75kW) on the original basis for providing compressed air in the workshop, and support the corresponding micro-heat adsorption dryers, filters, distribution cabinets and re-programming of the machine room pipelines. In order to improve the air quality of the compressed air system and achieve the purpose of energy saving. The main equipment of the permanent magnet frequency conversion air compressor replaced in this project is shown in Table 1 for its model specification and quantity.
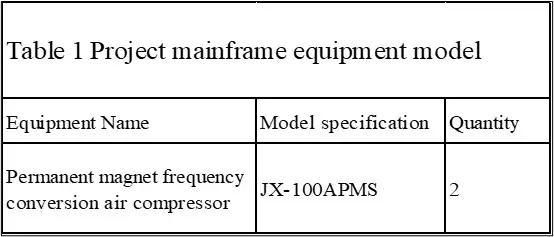
The JX-100APMS permanent magnet variable frequency air compressor selected for this project is mainly based on the following considerations: first, energy saving. Under localized load conditions, the maximum power COP of the unit can reach 12, and the annual energy saving effect of the system is about 10% higher than that of the original air compressor according to the budget calculation; Secondly, it is to improve the air quality. The quality of the original compressed air is upgraded by one level (containing dust, water and oil); Thirdly, the operation noise of the system is small. Permanent magnet frequency conversion air compressor design structure is compact, set with vibration isolation air cushion, so the noise of the air compressor selected for the project is below 75dB; Fourth, low operating current. The permanent magnet frequency conversion screw air compressor regulates the supply according to the air demand of the production plant. The original compressor starting current needs 500A, running current can be as large as 173A. However, after the update of the permanent magnet frequency conversion screw air compressor, due to its use of frequency conversion soft start, the required starting current is less than 6A, the maximum does not exceed 127A, and can be adjusted according to the site’s air supply demand. There is no need to design grid protection measures.
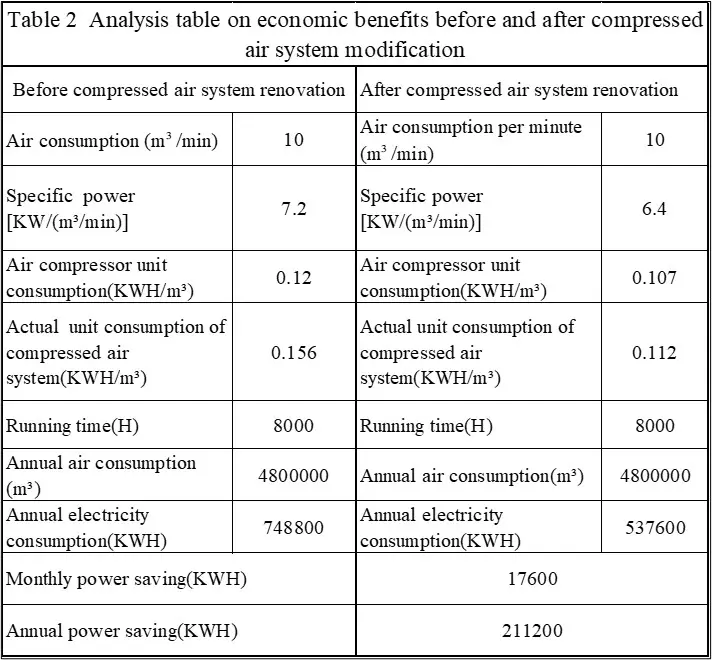
5. Reform benefit analysis
After the stable operation in the early stage, the overall energy consumption of the air compressor has been significantly reduced, and according to the current real working condition, the efficiency COP of the air compressor has reached 2.0, which produces good energy-saving effect; after the completion of the project, it can improve the quality of compressed air, ensure the safety of compressed air, meet the GMP standard and realize the expected purpose.
5.1 Economic benefits
The economic benefits of the compressed air system before and after the modification are detailed in Table 2. Note: The above data was provided by the metrology department. The project was officially started from April 2022 and completed in August 2022, which lasted 4 months. After the comparison of the above information, it is estimated that the average monthly energy saving of the system after the renovation is about 17,600.00kW/h, and the annual energy saving of compressed air supply electricity for the company after the completion of the project is as high as 211,200.00kW/h. From the above data, it can be seen that the revamped compressed air system has obvious economic benefits; compared with the previous years, it is estimated to save the consumption of electrical energy of 210,000 kW/h, and the estimated number of years for cost recovery is: 742,334 yuan × 211,200 yuan/3.51 years, which realizes the expected goal of the project; the old compressed air system has been used for nearly 20 years, and the comprehensive energy consumption will be greatly reduced, and the unit consumption will be increased in accordance with the ratio of the coefficient of 1.3; the unit consumption of the new compressed air system will be increased in accordance with the ratio of the coefficient of 1.05,at the same time, as the company’s production output continues to increase, saving more electricity and energy consumption, the economic benefits are more significant.
5.2 Social benefits
(1) The successful application of this project has greatly improved the quality of compressed air and ensured the safety performance of air compressors. The renewal of air compressors not only facilitates the safe operation of equipment, but also effectively promotes automated equipment management as well as training of maintenance skill levels and technicians; to comply with the national policy of energy conservation and emission reduction, reduce the production cost of enterprises, and make its own contribution to society.
(2) To ensure to a greater extent that the quality of pressurized air in the enterprise meets the requirements of the GMP standard, and to ensure that the drugs produced in this environment meet the relevant standards stipulated by the state, to be responsible for the society and patients.
6. Conclusions
Air compressor is an indispensable air compression equipment in the pharmaceutical industry, but at present the air compressor is commonly used in fixed-frequency operation, which leads to high energy consumption and increased carbon emissions in the environment, so it is not conducive to energy saving and emission reduction of pharmaceutical companies, and it makes the wear and tear of the equipment greatly accelerated, impairing the economic benefits of enterprises. The use of frequency conversion mode of operation can make it reach the most economical working condition and can effectively realize the automatic constant pressure supply of air pressure, making the equipment more durable, thus ensuring the quality of drugs and improving the economic benefits of pharmaceutical companies.
Our company has carried out certain analysis on the energy-saving transformation of air compressors: we not only introduced the basic technology of permanent magnet frequency conversion air compressor and its features of low noise, long life and low energy consumption, but also took a certain pharmaceutical enterprise as the research object, transformed its old air compressor into permanent magnet frequency conversion air compressor, and analyzed the actual application effect of permanent magnet frequency conversion air compressor. The result proves that compared with the traditional mechanical fixed-frequency screw air compressor, the permanent magnet frequency conversion screw air compressor has the advantages of environmental protection and energy saving, durability, and small size. Therefore, in the future development, the permanent magnet frequency conversion screw air compressor will have a broader application prospect. Click here to read blog.