An Overview of the Influence of the Characteristics of Oil Injections on the Thermal Performance of Screw Air Compressors
2024-04-03
Screw air compressor is a kind of positive displacement compressor with unique advantages of high reliability, easy operation and maintenance as well as good power balance, which is widely used in air power and other industrial fields. When the air compressor is in operation, the appropriate amount of lubricating oil sprayed into the compression chamber can form a good oil film between the rotors, which can effectively reduce the friction between the rotors in time. However, the sprayed lubricant increases the friction of the air compressor and increases the power consumption of the air compressor. Analyzed theoretically, the air compressor should have the optimal amount of oil injection. In addition, through the implantation of frequency converter to control the speed of the motor in the compressor group, although it can realize the regulation of the exhaust volume of the air compressor, so that the performance of the screw air compressor is more superior, the relative leakage of compressed gas varies with the change of the speed of the compressor, which affects the performance of the compressor as well, in order to make the compressor in the best performance of the different speeds, we should install the oil volume adjustment device in the oil circuit system of the air compressor.
1. The lubrication system and oil injection characteristics of screw air compressor
1.1 Composition of lubrication system
Screw air compressor oil system is mainly composed of air compressor body, oil-air separator, oil cooler, temperature control valve and oil filter, etc. The air compressor lubrication system is shown in Figure 1. Some screw air compressors are also installed at the exhaust port in the way of temperature sensors, replacing the temperature control valve, and by the main inverter to directly monitor and control the exhaust temperature and oil discharge temperature. In the working process of the air compressor, after the air is compressed to a specific state in the cavity of the air compressor, the lubricating oil is sprayed in from the oil injection orifices and mixes with the compressed air to form an oil-air mixture in the intertooth volume. Therefore, the compressed air will contain a large number of oil droplets, the gas mixture of high temperature and high pressure discharged from the exhaust port of the compressor needs to enter the oil-air separator, after separation, the lubricating oil has to pass through the oil cooler and oil filter and then sprayed into the compression chamber to complete the whole cycle.
However, the efficiency of the oil and gas separator can not reach 100%, in order to maintain the balance of the lubricant required in the air compressor, the system needs to provide the appropriate amount of lubricant to the suction side of the screw compressor that is the amount of oil back to meet the conditions of the oil back, when the exhaust is not less than the amount of oil, the air compressor oil system cycle will run smoothly.
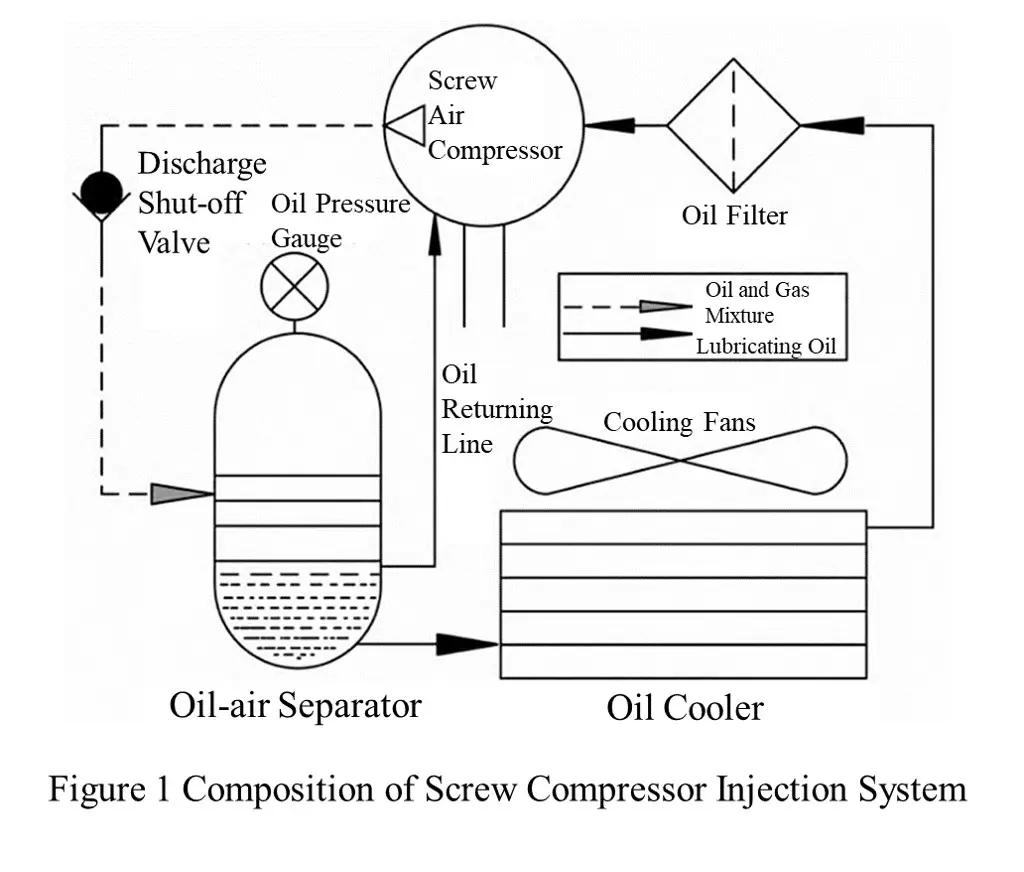
Minimum pressure valve is usually installed in the oil-air separator of screw air compressor oil circuit system to establish the internal pressure of air compressor group, promoting the circulation of lubricating oil in the oil circuit system, meeting the working pressure of the relief valve, and avoiding the harm of pressure difference to the separator. The reason for the existence of the Minimum pressure valve is that the lubricant supply of the compressor is carried out by the pressure difference of the compressor itself, and no additional oil pump is set up. When the compressor is in the unloaded state, the compressor still needs a certain amount of pressure to maintain the circulation of the oil system, so the compressor inlet valve is relatively closed, and the minimum pressure valve prevents the pressure from leaking, which guarantees the circulation of the lubricating oil in the air compressor. In addition, the minimum pressure valve also plays the role of a check valve, which can prevent the air compressor in unloading operation when the air backflow.
1.2 Calculation of lubricant quantity
For the whole compression process of oil-injected screw air compressor, if the exhaust temperature is given, the theoretical oil injection volume of the screw air compressor can be determined by the thermal balance of the air compressor, and vice versa, if the parameters such as the oil injection volume are determined, the theoretical exhaust temperature can also be found. According to the law of conservation of energy, the heat balance of the compressor is as follows:
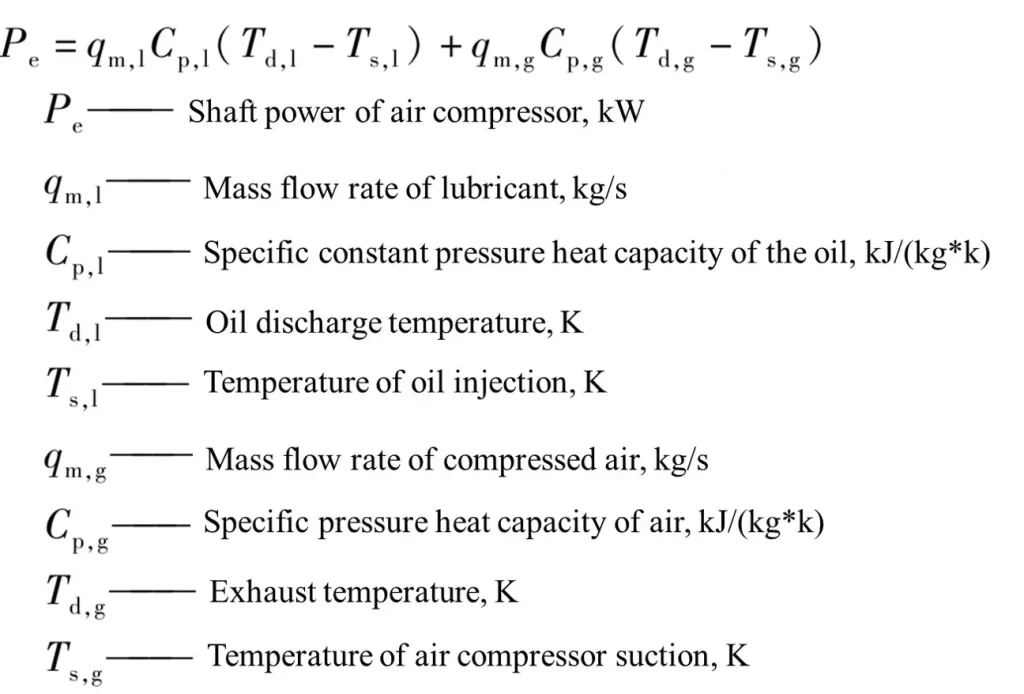
In the theoretical calculation process of screw air compressor oil injection, generally assumed that the oil discharge temperature and exhaust temperature is the same, and that the process does not lose heat to the outside world. In the actual compression process because of the heat transfer temperature difference between the lubricant and the air, the calculation results will inevitably produce the corresponding deviation, the details also need to refer to the experimental data to be corrected. It is worth noting that, in addition to spraying oil into the rotor tooth volume, screw compressor bearings and shaft seals also need a corresponding amount of lubricant. Because air is virtually insoluble in oil, all the oil supplied to the compressor ultimately plays a role in controlling the exhaust temperature, but the path of transmission is different. The formula is only theoretically determined purely by considering the heat transfer of the amount of oil injection, in the actual simulation and calculation, but also need to take into account the impact of leakage and power consumption and other factors.
1.3 Degree of spray atomization
In the working process of the screw air compressor, the lubricant sprayed into the cavity of the air compressor enhances the heat exchange of the compressed medium, and plays the role of lubrication, sealing and noise reduction. For different working media, the lubricant sprayed into the cavity of the air compressor must be different categories and physical properties. When choosing lubricants for air compressors, in addition to considering the viscosity of the lubricant, we also need to consider the lubricant’s oxidation resistance, anti-foam, corrosion resistance and anti-emulsification and other indicators.
In the process of oil injection, the viscous force of the lubricant itself, the air resistance it is subjected to and the surface tension of the oil play a major role in the mechanism of oil injection fragmentation. The air resistance in the compression chamber makes the larger oil droplets injected into the twisted deformation, and combined with the friction between the oil and the compressed air, the parts protruding from the surface of the oil droplets formed due to the internal perturbation of the oil droplets will be split and under the action of the surface tension of the oil it forms a smaller oil droplet. Obviously, the air resistance needs to overcome the combined force of surface tension and viscous force to make the oil droplets twisted and deformed, dispersed oil droplets, until their combined force reaches the equilibrium state.
In addition, the parameters affecting the oil spraying process of the screw air compressor also include the position and diameter of the oil spray orifice, the oil spray temperature and the oil spray volume, etc., which all directly or indirectly affect the atomization effect of the oil spray. In the screw compressor usually use the size of the Vibro number to determine whether the degree of lubricant atomization is good or bad, in which the atomization form of oil droplets can be divided into droplet liquid flow, smooth liquid flow, corrugated flow and spray flow. Obviously, under the premise of meeting the sealing of the air compressor, the spray flow can be fully exchanged for heat with the compressed air with the best effect.
2. The effect of oil injection characteristics on the performance of Screw Air Compressor
2.1 Influence on exhaust temperature
Compared with the dry screw air compressors, the injection of lubricating oil into the screw air compressor performance has changed greatly, simplifying the structure, improving the pressure ratio, controlling the exhaust temperature and reducing the noise. The exhaust temperature of the oil-injected screw air compressor is no longer determined by the pressure ratio and the physical properties of the air, but is determined by the combined effect of the lubrication system, the oil injection volume, the compressor speed, and the specific volume of air. According to the theoretical oil injection volume formula, if the oil injection volume is enough and the oil injection temperature is low enough, the exhaust temperature of the compressor can be lower than the inlet temperature. In frequency conversion air compressor, when the air compressor running speed is relatively high, the friction between the rotor is relatively large, the heat exchange between the lubricant and the compressed air is not sufficient, and the theoretical exhaust temperature should be relatively high under the same amount of oil injection.
2.2 Effect on volumetric efficiency
Volumetric efficiency is one of the important indicators of the operating characteristics of air compressors. The volumetric efficiency of the oil-injected screw air compressor reflects the perfect degree of utilization of the air compressor geometry. The actual volumetric flow rate and volumetric efficiency of the oil-injected screw air compressor can be calculated through theoretical calculations. The volumetric efficiency of the screw air compressor is limited by many factors such as the type of profile, differential pressure and rotational speed. The injection of lubricating oil plays a good sealing effect on the multiple leakage channels of the air compressor, which significantly reduces the leakage and improves the volumetric efficiency. When theoretically analyzing the screw air compressors run at variable speed, the higher the speed is under the same amount of oil injection, the higher the volumetric flow is, the better the sealing effect is, and the higher the theoretical volumetric efficiency should be; when the rotational speed is constant, the increase in the amount of oil sprayed should make the volumetric efficiency increase gradually, but the influence of the oil return in the compressor can not be ignored.
2.3 Impact on insulation efficiency
Adiabatic efficiency is another important indicator of air compressor performance, reflecting the perfection of energy utilization of the air compressor. The isentropic adiabatic power of the oil-injected screw air compressor can be calculated by the following formula, when the compressed air is treated as an ideal gas. The ratio of the isentropic adiabatic power to the actual shaft power of the compressor is the adiabatic efficiency.
In the working process of the air compressor, the lubricant plays a sealing role at the same time also by the friction of the rotor churning oil, which needs to absorb a certain amount of work. Obviously, the amount of power consumption is closely related to the size of the injection volume, compressor speed and lubricant viscosity. Theoretically, for the adiabatic efficiency, the constant speed of oil injection should have the best value; when the frequency conversion air compressor runs, the rotational speed and oil injection should be accurately coordinated, so that the air compressor performance will be optimal.
3. Conclusion
Our company mainly introduces the screw air compressor oil injection system, parameters of oil injection and the impact of atomization characteristics on the performance of the air compressor. The injection of lubricating oil not only reduces the exhaust temperature, but also improves the efficiency of the air compressor. PM VSD screw air compressor can change its volumetric flow rate by changing the rotor speed, so the oil injection air compressor should run in reasonable cooperation with the speed. The ideal oil injection volume of screw air compressor should be practically corrected on the basis of theoretical calculation. The oil spraying aperture, oil spraying volume and oil spraying pressure of the screw air compressor determine the degree of atomization of the lubricating oil, and the spraying flow with the best heat exchange effect should be adopted in practice under the premise of meeting the sealing of the air compressor. The performance of frequency conversion air compressor is more closely related to the operating characteristics of the oil spray, targeting the oil volume adjustment device can make the frequency conversion air compressor in different speeds under better performance.