The stability and reliability of the Screw Air Compressor Motor, as an important public utility for the energy supply of the production system, is of utmost importance. A steel company adopts Ingersoll Rand screw air compressor, which has been put into use since 2011, and the system has been running stably, and the gas production and energy consumption have been kept in the normal state.
Since July 2015, there have been several accidents of motor burnout in the air compressor station, which brought greater impact on production because the cause of the failure is difficult to be characterized. By analyzing the factors that may lead to accidents, summarizing the reasons for such accidents, and implementing a series of rectification measures, the company has provided guarantee for the stable operation of air compressors in long cycles.
1. The current situation of the Screw Air Compressor Motor and failure phenomenon
There are 7 Ingersoll Rand screw compressors in the station, with two models, M250-HV and M300-HV, which adopt a monthly switching system, with 4 openings and 3 standbys, and each compressor has an independent control system, and no centralized monitoring system is set up in the station.
In July 2015, during the normal startup process of the air compressor motor, it triggered an accident of tripping of the 10kV switch at the upper level, and after on-site inspection, the insulation breakdown of the A phase of the air compressor motor led to motor burnout.
Later, after the transformation and rectification of the electric control circuit, one year after the system was running stably, five more air compressor motor burnout accidents occurred, and after the motor was disassembled and analyzed, all of them were found to have traces of one-phase or two-phase winding burnout of varying degrees.
2. Analysis of causes and corrective measures: Screw Air Compressor Motor
The motor burned out in July 2015 to access the air compressor control panel fault records, all parameters are normal, fault records show that “the main motor overload”. In the 10kV high-voltage background monitoring system, there are four records of “overflow action”, indicating that the air compressor station motor has a frequent continuous start phenomenon. Preliminary analysis, that the high-pressure switch action, the signal and the air compressor control stop signal interlocking protection failure, the high-pressure switch did not open the gate in time to play a protective role, causing the motor to continue to overload and burned.
High-voltage motor start and stop is controlled by the high-voltage switchgear, through the air compressor 10kV high-voltage system overcurrent protection faults and contactor operation status check and analyze, confirm that there is no fault in the control cable and the signal can be normally connected, open and close. However, when simulating a high-voltage fault, the compressor does not respond to the fault shutdown signal.
A shutdown inspection of the other six air compressors revealed the same problem. After communicating with the manufacturer, when ordering the Ingersoll Rand air compressor equipment, the high-voltage control cabinet was not purchased, but the original high-voltage electrical cabinet of the plant was utilized. In the process of use, the interlock signal function between the low voltage control of the air compressor and the high voltage cabinet supplying power to the air compressor was not connected, which led to the failure of the electrical interlock signal of the air compressor, affecting the safe and stable operation of the air compressor.
Analysis that the air compressor electrical interlock signal power supply from the air compressor control unit 24 V power supply, 24 V power supply capacity and cable laying environment, length and other impacts, There may be strong interference with the 24 V feedback signal from the magnetic field generated by the power cables on the cable tray, which generates false signals and prevents reliable transmission of the signal, in order to ensure that the air compressor signal is normally transmitted to the air compressor electric control circuit to be In order to ensure the normal transmission of the air compressor signal, the air compressor electronic control circuit is modified to eliminate the signal defects, the specific measures are shown in Figure 1.
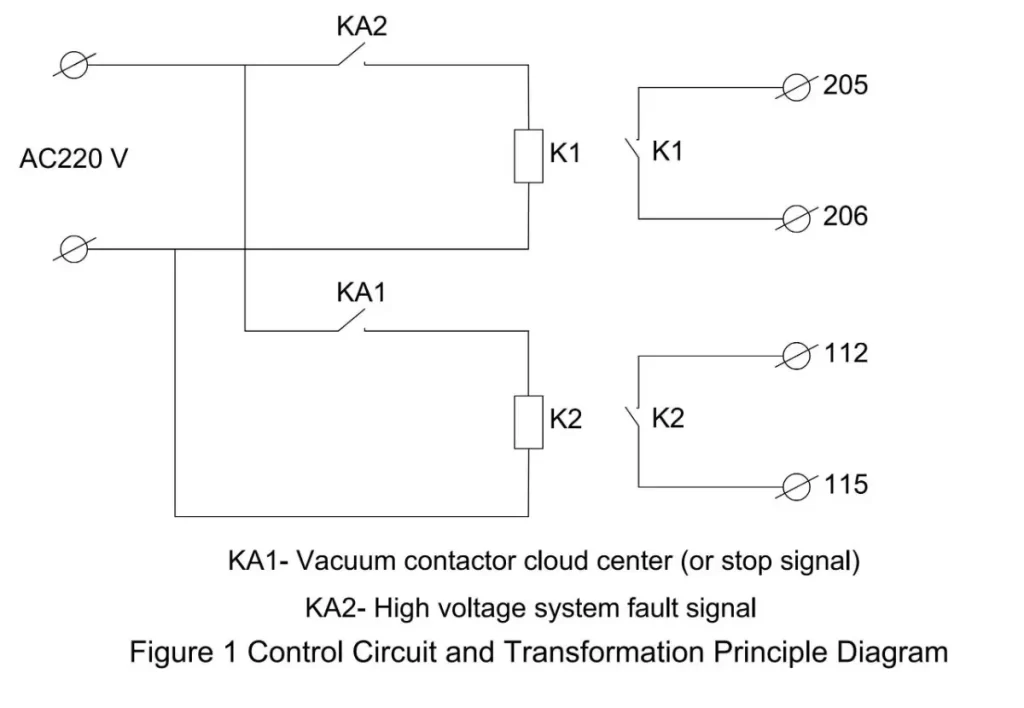
(1) Strictly in accordance with the nature of the cable transmission classification, high-voltage power, low-voltage power, control signals laying in layers, to avoid mutual interference of different signals of the cable, to reduce the source of interference. To this end, the use of twisted shielded control cables, and power cables separate, separate laying.
(2) High-voltage signal transmission power supply voltage using DC24 V power supply, 10 kV high-voltage signal cable has a certain induction voltage, easy to signal abnormalities, considering the site conditions, in order to improve the signal interference resistance, high-voltage signal transmission power supply voltage from DC24 V to AC220 V.
(3) In the field control cabinet of the air compressor, two intermediate relays are added to improve signal reliability and accuracy of signal transmission. After the implementation of the above control loop modification, before putting into operation, in the 10 kV high-voltage cabinet to do analog signal test, air compressor electric control cabinet control unit are signal display information. In the actual operation process, the air compressor high-pressure electrical cabinet signal and air compressor control cabinet signal between the signal loss phenomenon did not occur, there is no motor has a frequent continuous start and the phenomenon of signal interlocking protection failure, improve the accuracy and reliability of the signal feedback function, the motor has played a certain role in protecting the motor to solve the motor burned out caused by this problem.
In the exclusion of the electric control caused by the motor burn factors, followed by several motor burn accidents, for the various factors that may lead to accidents to carry out a comprehensive analysis of the study, and strive to find other causes of accidents, from the fundamental solution to the motor burn accidents in the air pressure station.
3. Main causes and measures for motor burnout failures
After the burnt 7 sets of motor disassembly maintenance, common problem is the burnt part for the winding of a phase of a local burn phenomenon. In view of this problem, the main reason is centered on the frequent starting of the motor and the influence of external environmental factors, resulting in frequent burning of the motor.
3.1 Frequent motor start
Due to the requirements of equipment management, the standby equipment is required to be rotated regularly to ensure that the equipment is in good condition and can be reliably put into use when the mainframe fails. The actual provisions on site provide for the commissioning of standby equipment at 7-day intervals, after normal operation, as the host into use, and at the same time the corresponding deactivation of another host, week after week, the cycle of casting and cutting. As the 10 kV high-voltage motor of the air compressor, the direct starting method is adopted, and the actual starting current reaches more than 7 times of the rated current, which will lead to the following consequences for the motor:
(1) Due to the motor overload or overheating operation for a long time, there is a certain stator winding coil insulation aging phenomenon, the weakest point of the insulation is easy to carbonization triggered by local grounding, inter-wire short-circuit, or turn-to-turn short-circuit and other faults, resulting in localized burning of the winding coil.
(2) motor stator coil in operation due to the role of electric power (such as start-up high current impact, the vibration of the drag equipment, etc.), resulting in winding coil loose wear phenomenon, long-term high potential will also make the stator coil corrosion, such as insulation embrittlement, cracking of the insulation and other phenomena, resulting in the destruction of the first carbonization of the insulation until the burning of the winding coil.
3.2 External environmental factors
The Screw Air Compressor Motor plant is close to the ironmaking plant, and the plant is not closed tightly, so iron chips and iron powder enter the plant. Operators use water pipes to clean the ground instead of daily cleaning work, coupled with poor indoor ventilation, moisture is too large, water vapor can not be removed. As the motor itself is not well sealed, moisture, dust or other corrosive gases, penetrate into the insulation inside the motor, so that the stator coil localized moisture or erosion, reducing the winding insulation strength, which leads to localized burnout of the motor winding. Especially for the shutdown state of the air compressor, moisture, and dust into the motor to reduce the motor insulation, more likely to start the motor burned accident.
4. Treatment measures: Screw Air Compressor Motor
The following corresponding measures have been developed for the air pressure station equipment:
(1) Revise the management system for the operation of air compressor standby equipment and minimize the number of times the high-pressure motor is turned on. Reverse the operation every half a year on the standby equipment for power supply test, daily only on the standby equipment regular disk, inspection and other routine maintenance work, especially to reduce the number of short intervals in the hot state of the number of start-up, start-up interval time for more than 30 min.
(2) Strengthen the inspection of insulation and cage strips in the major and minor repairs of the motor and replace or dip epoxy resin paint on the cracked and aged parts of the stator windings; reinforce and replace the loose and fatigued rotor cage strips.
(3) It is prohibited to use water to clean the ground in the air pressure station to avoid water vapor from entering the inside of the motor winding, and at the same time, non-woven cotton filtering cloth is added to the indoor shutters to prevent iron filings and dust from entering.
(4) Do a good job of ventilation and heat dissipation of the motor itself and the surrounding environment to ensure a good operating environment for the motor.
(5) Do a good job of sealing each part of the motor, such as applying a small amount of sealant to each flange to prevent oil from entering the motor windings.
5. Effectiveness of implementation
The implementation of targeted measures to solve the Screw Air Compressor Motor burning accident, to ensure the safe operation of the motor for a long period of time, and to improve the stability and safety of the air compressor operating system. In addition, there are some other reasons that can cause the motor to burn, it is important to take the following precautions to ensure the normal operation of the air compressor.
(1) By the control cabinet relays, high-voltage cabinet switches, integrated protection (including undervoltage, quick-break, overcurrent, and other basic protection.) failure, resulting in motor burnout problems.
Countermeasures: Relays and switchgear should be tested regularly, and problems should be repaired or replaced in time.
(2) Due to bearing wear and other reasons resulting in stator and rotor friction, the phenomenon of sweeping, resulting in a sharp rise in core temperature, burned slot insulation, turn-to-turn insulation, resulting in a short-circuit between the turns of the windings or the phenomenon of the ground “gun”.
Countermeasures: the service life of the bearings has reached 5 years for replacement; regular refueling, prohibit a variety of lubricating grease mixing; bearing temperature monitoring.
(3) The motor burnout fault caused by the supply voltage phase loss should be emphasized. Because the motor is running after the phase is still able to run, just the magnetic field distortion, but the speed drop, the slip becomes larger, in the case of the load is unchanged will lead to a phase current is too large, when a long time after the operation of the phase winding may be due to overheating and burned.
Countermeasures: routine maintenance and overhaul of the motor at the same time, the motor for the appropriate vacuum contactor contacts check and test, including power line reliability, to eliminate phase missing operation.
6. Conclusion
For the Screw Air Compressor Motor failure in operation, should attract enough attention, maintenance personnel should be able to quickly and accurately analyze the problem and solve it in a timely manner. To do a good job of daily monitoring of the operating status of the unit, timely maintenance of the key parts of the maintenance, to extend the motor insulation aging cycle and the service life of the air compressor, to really do the prevention, to maintain long-term stable and efficient operation of the equipment. Click here to read blog.