Research on the Application of Permanent Magnet Motor on Screw Air Compressor
2024-03-04
Compressed air has become one of the most widely used power sources in the industrial field because of its characteristics of easy storage, easy control, good fluidity and safety, environmental protection, etc. It is widely used in many fields such as electric power, textile, chemical industry, pharmaceutical industry, electronics, metallurgy, and machinery manufacturing. Because of the high cost of air compressor energy operation, improving the effectiveness of air compressor operation has gradually attracted the attention of enterprises. For example, a volume flow rate of 20m³/min rated exhaust pressure of 0.8 MPa air compressor, the annual electricity costs up to 900,000 RMB, the entire life cycle of five years, then the cost of electricity will be as high as 4.5 million RMB, coupled with the usual cost of repair and maintenance costs, the cost of the lifecycle will be as high as more than 5 million RMB; and the cost of equipment purchase ranges from $80,000 to $200,000, which is only 2% to 5% of the cost of use. Therefore, improving the energy efficiency of Permanent Magnet Motor air compressor operation can not only save a lot of energy running costs for enterprises, but also achieve energy saving and emission reduction.
1. Status of air compressor operation
We investigated 1,000 key power-using enterprises in a city that consume more than 5 million kWh of electricity annually, and found that the power consumed by air compressors accounted for an average of 12% of the total power consumption of the enterprises (see Figure 1), and up to 30% or more in some of the enterprises, in which screw-type air compressors are most widely used. Most of the compressed air systems in use have low operating efficiencies, and there are problems such as mismatched equipment, large piping losses, system leakage, and irrational system control.
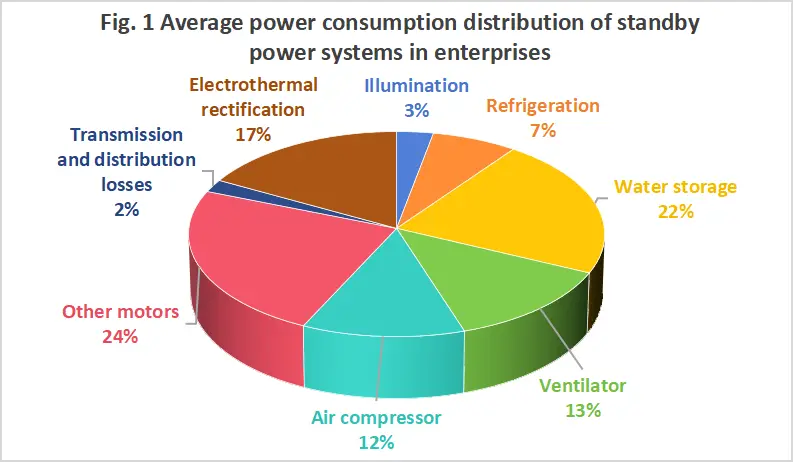
At present, through the government’s vigorous promotion and the continuous innovation of enterprises, the development of energy-saving technology of air compressors is gradual and rapid.Energy-saving modifications mainly include frequency conversion speed control, waste heat recovery, linkage control, pressure control and piping optimization, etc. Most users seeking to maximize the energy savings of air compressors must be achieved through the combined use of a variety of energy-saving methods. Although there are more technologies for energy-saving transformation of air compressors, there are fewer cases of transformation for improving the energy efficiency of air compressors themselves. With the continuous improvement of domestic electric motor energy efficiency, it is an effective way to improve the energy efficiency of air compressor operation by reforming the supporting electric motor of the air compressor.
According to the U.S. Department of Energy’s 2002 research report, air compressors used in various countries, its load factor is almost impossible to exceed 90%, therefore, in addition to the air compressor full load to have a high energy efficiency, when in part of the load and no load, effectively saving energy is even more important! According to industry survey data, the average load factor of domestic air compressor is about 57%, based on this working condition, the direct drive motor screw air compressor on the market is very energy-consuming, and the use of frequency converter to drive the motor, by adjusting the speed of the motor to achieve the adjustment of the volume of air is a major step forward in the air compressor industry. This method saves some power, but when the motor speed decreases, it is not yet the optimal matching motor for frequency conversion air compressor because the ordinary three-phase asynchronous inverter motor is designed based on the rated power point, which will cause a sharp decrease in the motor power factor and efficiency.
2. Advantages of permanent magnet compressors
In recent years, with the rapid development of rare-earth permanent magnet materials, permanent magnet synchronous motors have been rapidly popularized and applied, which have the advantages of small size, low loss, high efficiency, etc., and are widely used in many industries. Permanent magnet synchronous motor has the following advantages compared with ordinary asynchronous frequency conversion speed control motor:
2.1 High efficiency
The high efficiency referred to here does not only mean that the efficiency at the rated power point is higher than that of an ordinary three-phase asynchronous FM motor, but also refers to its average efficiency over the entire speed regulation range. The excitation field of permanent magnet synchronous motor is provided by permanent magnet, the rotor does not need excitation current, the efficiency of the motor is improved, and compared with the asynchronous frequency conversion speed control, any point of the speed can save electricity, especially in the lower speed when this advantage is more obvious.
2.2 Small starting current and large starting torque
According to the V/F characteristics of the inverter, at low frequency startup, the main magnetic field in the asynchronous frequency control motor is low, the power factor is low, the startup current is very large, and the startup torque is very small; the main magnetic field of the rare-earth permanent magnet synchronous frequency control motor is constant, and almost all of the stator current is active, so the startup current is small and the startup torque is large.
2.3 Good force-energy indicators
The force-energy index of a motor is the product of motor efficiency and power factor. When an asynchronous frequency-controlled motor is operated at 60 percent load, its efficiency decreases by 15 percent, its power factor decreases by 30 percent, and its performance index decreases by 40 percent. The efficiency and power factor of the rare-earth permanent magnet frequency conversion motor approximate a horizontal curve, even if the motor is only 20% of the load, the rare-earth permanent magnet motor’s power index is still more than 80% of the full load, which further improves the efficiency of the use of electric energy and the quality factor of the power grid.
2.4 Small size and light weight
High-performance permanent magnet materials provide the magnetic field, so the air gap magnetic field of permanent magnet motors is greatly enhanced compared with induction motors, and the size and weight of permanent magnet motors are greatly reduced compared with induction motors.For example, while an 11 kW asynchronous motor weighs 220 kg, a PM motor weighs only 92 kg, which is 45.8 per cent of the weight of an asynchronous motor.
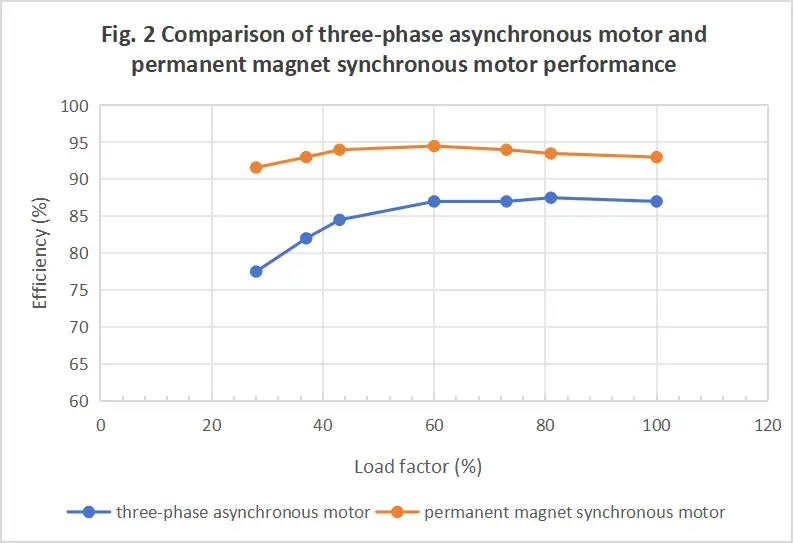
Figure 2 is a comparison of the efficiency values of a 5.5kW ordinary three-phase asynchronous motor and a permanent magnet synchronous motor at different load rates. It can be seen from the figure that the difference in efficiency between the three-phase asynchronous motor and the permanent magnet synchronous motor is about 5%, which is an advantage that becomes even more obvious in the low-speed operating range.
Based on the above comparative advantages, at present, permanent magnet motors are the best choice for inverter screw compressor drive motors, which are more efficient and energy-saving than ordinary three-phase asynchronous inverter motors.
3. Permanent magnet compressor application case study
We take the same 160 kW screw compressor as an example to calculate, the efficiency of permanent magnet motor is about 97%, the efficiency of ordinary motor is about 90%; according to the efficiency of the permanent magnet motor energy saving of 7% and the average air consumption of 90% for calculation, considering the service coefficient of 1.15, then in the case of 90% of the air output condition of the motor hourly power consumption saving amount is:
160kW×1.15×90%×7%=11.592kW
According to working 16 hours per day, running 300 days per year, and the average industrial electricity consumption is 1 RMB/KWh, The annual savings in electricity costs would be approximately:
16 x 300 x 11.592 x 1 = 55,641.6 RMB
Under normal conditions, the cost of permanent magnet motors is about 80,000 RMB, and basically the increased investment cost can be recovered in 1.5 years. If the compressor runs under low load conditions for a long time, the energy-saving benefit is even more obvious.
4. Conclusion
Air compressor, as a large energy consumer in the motor system, will become a key area of China’s industrial energy saving in the future, energy-saving air compressor has been listed as the energy-saving products to promote the project in 2013 by China, indicating that the use of high-efficiency air compressors has been the development trend. With the gradual reduction of the price of permanent magnet motor, with its superior performance, permanent magnet screw air compressor will become a new energy-saving bright spot in the air pressure industry. Read here.