Study on Over-temperature Shutdown of Oil Injection Screw Air Compressor
2024-03-29
Oil-injected screw air compressor is a rotary compressor, as a power source, compressed air has safety, economy, high efficiency characteristics, whether the oil-injected screw air compressor is in good operating condition directly affects the operation of the compressor. if the air compressor system fails, it will lead to compressor shutdown, resulting in the cessation of gas production at the site and affecting the gas consumption of downstream users, which will lead to very serious consequences. Our company analyze the reasons for over-temperature shutdown of the Oil Injection Screw Air Compressor and propose the solutions to ensure the safety operation in summer.
1. Problems in the operation of Oil Injection Screw Air Compressor units
At present, a total of four srew air compressors are in operation in an air compressor station, the motor power of 1# and 2# air compressors is 75kW, and the maximum instrumented air volume is 720m3/h, and the motor power of 3# and 4# air compressors is 90kW, and the maximum instrumented air volume is 900m3/h. During daily operation, 3# and 4# air compressors are operated alternately as the main air supply units, and 1# and 2# air compressors are operated alternately as auxiliary units.
Cooling fan is used to cool the compressed gas and coolant.
The temperature in the air compressor room can reach about 40℃ due to the hot summer, the highest temperature is above 33℃ from May to September, the temperature inside the compressor room rises, causing the suction and discharge temperature of the compressor to increase at the same time, and when the discharge temperature reaches 110℃, the compressor will be chained to shut down.
2. Causes
There are two factors that affect the shutdown of an air compressor due to high temperature alarms, the equipment and the environment.
2.1 Equipment factors
(1) The temperature measuring element is insensitive or faulty, resulting in a high exhaust temperature alarm.
(2) Clogging of the three components: air filter, oil filter and oil-air separator cartridge.
(3) Insufficient coolant addition or coolant emulsification.
(4) Failure of the temperature control valve, resulting in the coolant can’t be sufficiently cooled, directly back to the air end, resulting in high temperature and shutdown.
(5) Scaling inside the cooler, the thermal conductivity of the cooler is reduced, and the fan can’t be turned on for cooling.
(6) The cooler is externally clogged, resulting in a reduced cooling effect of the fan on the compressed air.
2.2 Environmental factors
Higher temperatures in summer lead to higher temperatures in the compressor room, resulting in high exhaust temperatures and shutdown of the compressor.
3. main causes recognized
(1) The temperature of air compressor room is too high.
(2) Scaling inside the cooler, the thermal conductivity of the cooler is reduced, and the fan can’t be turned on for cooling.
(3) The cooler is externally clogged, resulting in a reduced cooling effect of the fan on the compressed air.
4. Solution Measures: Oil Injection Screw Air Compressor
4.1 Reduce the temperature of the air compressor room
In order to reduce the temperature of the room, there are two solution measures. Firstly, open the air compressor room axial fan to increase the air compressor room ventilation, observation found that the temperature basically did not change. Secondly, close the door of the air compressor room, under the condition of ensuring the normal suction volume of the air compressor, close part of the window and install air conditioners to reduce the indoor temperature, which requires two air conditioners investment costs, as well as daily electricity and later air-conditioning maintenance and cleaning costs. This method is costly and not in line with the concept of cost reduction and efficiency.
4.2 Remove internal cooler scale with carbon cleaner
The UC-V205 is an efficient cleaning agent for removing severe carbon deposits without the need for heating and stirring. It has strong penetration capabilities and can clean dirt inside small and complex parts without manual intervention, while also preserving the precision of the components.
After the air compressor stops running, open the exhaust valve at the outlet of the air compressor to release the exhaust pressure to zero. Disconnect the coolant inlet and outlet hoses connected to the cooler, connect the coolant inlet of the cooler to the outlet of the circulation pump, place the circulation pump inlet into the open bucket of carbon cleaner, and put the coolant outlet hose of the cooler into the cleaning agent bucket. Start the circulation pump to clean the internal scale of the cooler with the cleaning agent for 2 hours. After cleaning and drying the inside of the cooler, reinstall the cooler hose fittings. Start the air compressor, and maintain the exhaust temperature of the air compressor at around 100°C. If the air compressor shuts down again due to high-temperature alarm within less than half a month of continuous operation, it indicates that the true reason for the high exhaust temperature alarm shutdown of the air compressor is not internal scaling of the cooler.
4.3 Use compressed air to purge radiators and add removable fans
Dust causes the amount of air blowing through the cooler to be reduced, resulting in poorer cooling. Use 0.7MPa compressed air to remove the dust in the cooler and add a mobile fan on the fan side to strengthen the cooling effect. After blowing and removing dust from the cooler, the cooling effect was improved, but the effect was not good, the exhaust temperature was still high, the air compressor continues to run for about 2 to 3 days, and then stops again.
4.4 Disassemble the radiator and clean it with a high-pressure water gun
During continuous operation, the air compressor’s cooler may accumulate oil and other contaminants, which cannot be completely removed by blowing, leading to a decrease in heat exchange efficiency and affecting the normal operation of the equipment.
Open the exhaust valve at the outlet of the air compressor to release the exhaust pressure to zero. Slowly open the coolant refilling port. Connect a draining hose to the drain valve connection at the bottom of the oil-water separator, and open the drain valve to drain the coolant from the air compressor oil-water separator. Once the coolant is fully drained, remove the outer protective cover and the cooler. Seal the four connections of the cooler with plastic tape to prevent water ingress. Use a high-pressure water gun to clean the cooler thoroughly, ensuring that all debris inside the cooler fins is removed. After cleaning the cooler, use a detergent to clean the blades of the cooling fan. Once cleaning is complete, restore the air compressor to its original state. Start the air compressor , the exhaust temperature of air compressor is maintained at 87℃, the effect is good.
5. Effective evaluation
Comparing the various cleaning measures of the air compressor, disassembling the radiator, and using a high-pressure water gun to clean it is the most effective.
Before and after the cooler is cleaned, two days with similar ambient temperatures are selected to compare the effect before and after cleaning.
5.1 Qualitative analysis of cooling effect
The effect of the cooler cleaning before and after the analysis, as shown in Table 1.

From the data in the table, it can be seen initially: the exhaust temperature of the air compressor before cleaning is 8℃ higher than the exhaust temperature of the air compressor after cleaning.
5.2 Quantitative analysis of cooling effect: Oil Injection Screw Air Compressor
The following assumptions are made.
(1) The heat generation Q of the air compressor remains unchanged during operation.
(2) The output power of heat sink fan remains unchanged.
In this case, the exhaust temperature of the air compressor is only related to the thermal conductivity of the cooler.
Set the thermal conductivity of the cooler area for A, the ambient temperature for T, the heat generated per unit time by the compressor unit during stable operation for Q, set the heat of the air compressor gas discharged before cleaning for Q1, set the heat radiator in the heat emitted by the air for Q2, set the heat dissipated by the heat exchanger lubricant for Q3, set the heat of the compressor gas discharged after cleaning for Q11, set the heat given off by the air in the radiator for Q22, set the heat dissipated by the heat exchanger lubricant for Q33, according to the law of conservation of energy, there is:
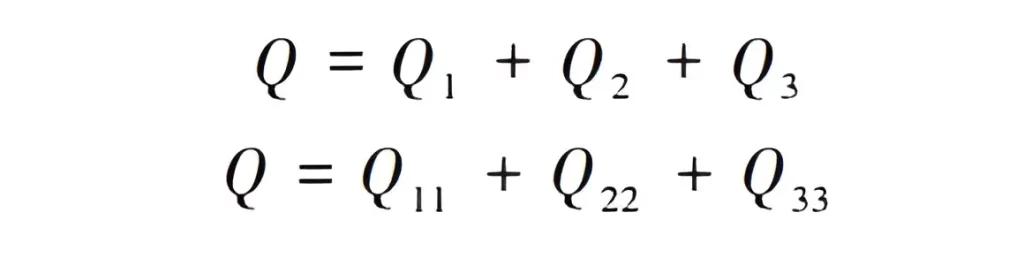

Assuming that the temperature of the exhaust air from the compressor remains the same before and after cleaning, and that the heat emitted from the air in the radiator remains the same, there will be: Q1=Q11, Q2=Q22 , So: Q3 = Q33
Due to:
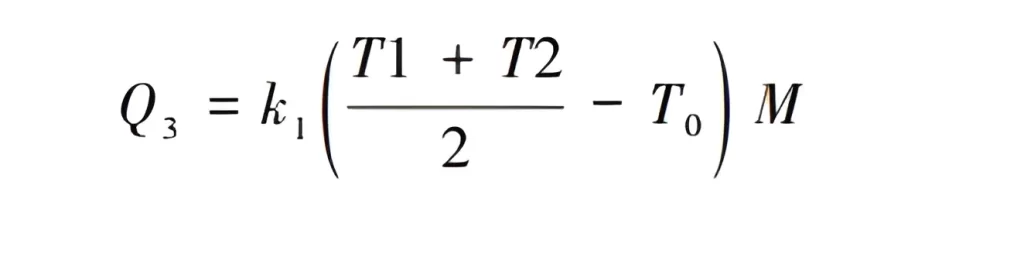
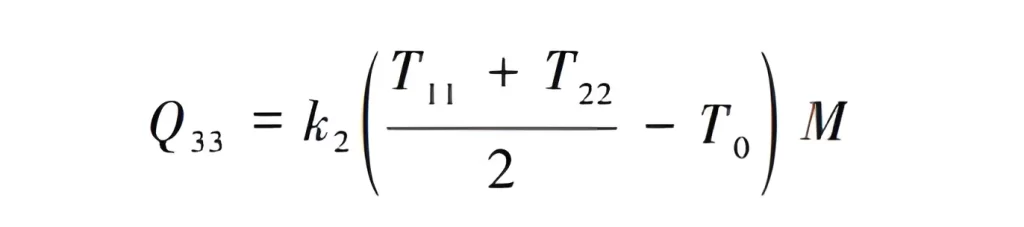
K1 is the heat transfer coefficient before cleaning, K2 is the heat transfer coefficient after cleaning, M is the mass of the lubricant, T1 is the temperature of the lubricant into the cooler before cleaning, T2 is the temperature of the lubricant out of the cooler before cleaning, T11 is the temperature of the lubricant in to the cooler after cleaning, T22 is the temperature of the lubricant out of the cooler after cleaning, T0 is the ambient temperature.
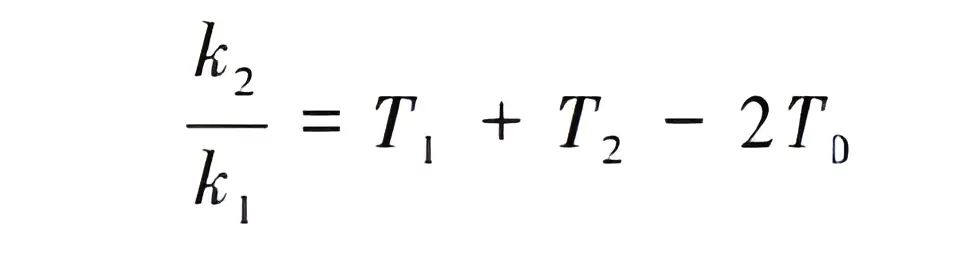
It is known that T1=102, T11=94, T0=31, so
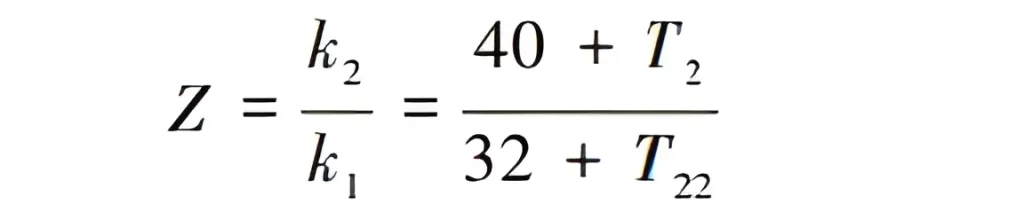
Since the air compressor has no coolant out of the cooler temperature probe, it is impossible to record the data accurately, according to the experience, the change interval of T2 and T22 is roughly in the range of 30 ~ 80℃.
The variation interval of heat transfer coefficient increase is shown in Fig. 1 as follows.
Because T2 is greater than T22, as can be seen from the figure, the heat transfer coefficients of the sections with Z-values greater than 1 are improved to some extent after cleaning.
In general, to solve the problem of high exhaust temperature and alarm during the operation of oil-injected screw compressor, disassemble the radiator and use high-pressure water gun to clean it, the effect is the best. Check new blog here.
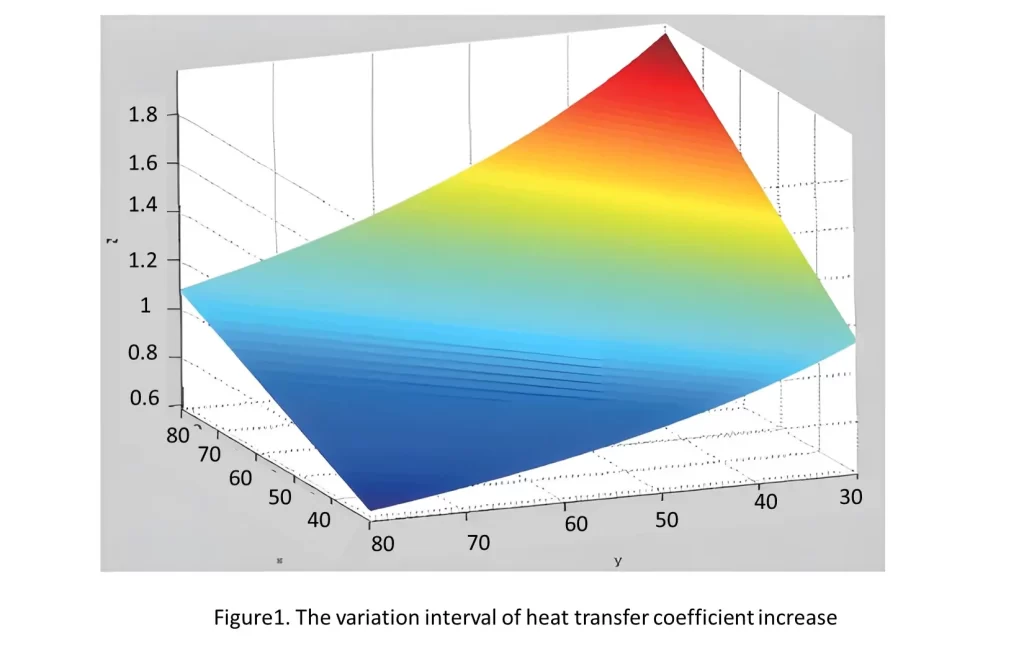