Economic Analysis and Technical Solution of Frequency Conversion Energy Saving Retrofit of Screw Air Compressor
2024-04-03
1. Overview
At present, Retrofit of Screw Air Compressor are widely used in various industrial and mining enterprises, and these devices are often the enterprise’s power consumption. According to our actual investigation of the users, the actual operating efficiency of these air compressors is generally low, only 50% to 70% or so, which is mainly due to two reasons: (1) design institutes and users in the selection often consider a larger margin, generally in more than 30%, which makes the actual operation of the screw compressor often shut down the inlet of the low load operating state, thereby reducing the operating efficiency; (2) ordinary screw compressors are in constant speed operation, but the actual production of gas demand is often in a state of flux, when the user reduces the amount of gas, the compressor unit can only be adjusted by all or part of the closed intake, so that the compressor unit will often be in the idling, part of the load (high-pressure than the state) and full-load operation of the low-efficiency state, resulting in a large amount of energy waste. Therefore, the operation of the Retrofit of Screw Air Compressor energy-saving problem is mainly manifested in the regulation of the exhaust volume, and the exhaust volume of the compressor is proportional to the speed of the compressor, so the problem of energy-saving screw air compressor is the problem of the speed control of the motor of the compressor. At present, small and medium-sized AC asynchronous motors for the best speed control method is frequency conversion speed control.
2. Operation Analysis of Retrofit of Screw Air Compressor
Retrofit of Screw Air Compressor is made of a pair of parallel meshing yin and yang rotors in the body to do relative high-speed rotary movement, so that the yin and yang rotor teeth groove forms a “V” shaped between the body and the continuous production of cyclical volume changes, the air along the direction of the rotor axis from the suction end of the delivery to the output end, realizing the suction, compression, and exhaust of screw air compressor. For an air compressor, within its design range, its exhaust volume is linearly proportional to its rotational speed. When the rotational speed rises, the displacement increases, the common screw air compressor can only run at a constant speed, but due to the initial design and selection of a relatively large air margin and the actual production of the air demand is often in a state of flux, so that when the user’s air consumption is less than the rated exhaust volume, the compressor’s supply pressure will rise, when the pressure rises to a certain pressure value above the user’s set pressure, the controller will close the inlet valve to stop the pressure from continuing to rise, and then the motor system is basically in the no-load state; in the no-load state, the compressor’s supply pressure will fall because the user is still using air, and the speed of its fall and rise again depends on the following two factors:
(1) The ratio of the user’s actual air consumption Q2 to the rated exhaust volume Q1 of the compressor. This value is expressed by λ, i.e. λ = Q2 / Q1 [0 < λ ≤ 1], the smaller λ, the slower the rate of pressure drops, but also indicates that the compressor in the no-load state running longer; the larger λ, the faster the rate of pressure drops, indicating that the air compressor in the no-load state will soon re-enter the load running state; when λ = 1, the system will not appear in the no-load and the load state alternatively, and has always been in the full load operation state.
(2) The user is the air compressor supporting the volume of the storage tank and the diameter and length of the pipeline. The larger the volume of the storage tank, the slower the rate of supply pressure drops and rises again, the lower the frequency of air compressor from the load state to the no-load state, thus reducing the air compressor due to frequent full-load and no-load conversion brought about by the additional power loss. But this does not eliminate the additional power loss caused by the imbalance of air supply and demand.
Figure 1 gives the trend graph of the relationship between power consumption and pressure variation of the air compressor at λ = 0.7, Q0 = 10Q1. Figure 2 gives the trend of the relationship between power consumption and pressure change of the air compressor when λ = 0.7, Q0 = 12Q1. Where Q0 is the volume of the air compressor tank, p is the minimum pressure to meet the user’s needs, Nz1 is the power consumption of the air compressor supply pressure at ps when running at a constant speed, ps + △ p is the maximum pressure of the air compressor operation, where △ p is the differential pressure of the pressure controller, Nz1 + △ Nz is the power consumption of the air compressor in the supply pressure of ps + △ p, Nz2 is the power consumption of the air compressor in the unloaded operation at a constant speed.
After comparing Figure 1 and Figure 2, it can be seen that after increasing the volume of the storage tank, the total trend of pressure and power consumption does not change, but only increases the alternating cycle between load state and no-load state. Through the above analysis, we can conclude that: most of the ordinary screw air compressor is mostly in the user’s minimum demand pressure above the load state and off the inlet of the no-load state between the alternating operation, and these two operating conditions are not the compressor’s efficient and economic operating conditions, the former due to the rise in exhaust pressure leads to torque increase, thus consuming too much power, the latter belongs to the no-load operation of wasting too much power.
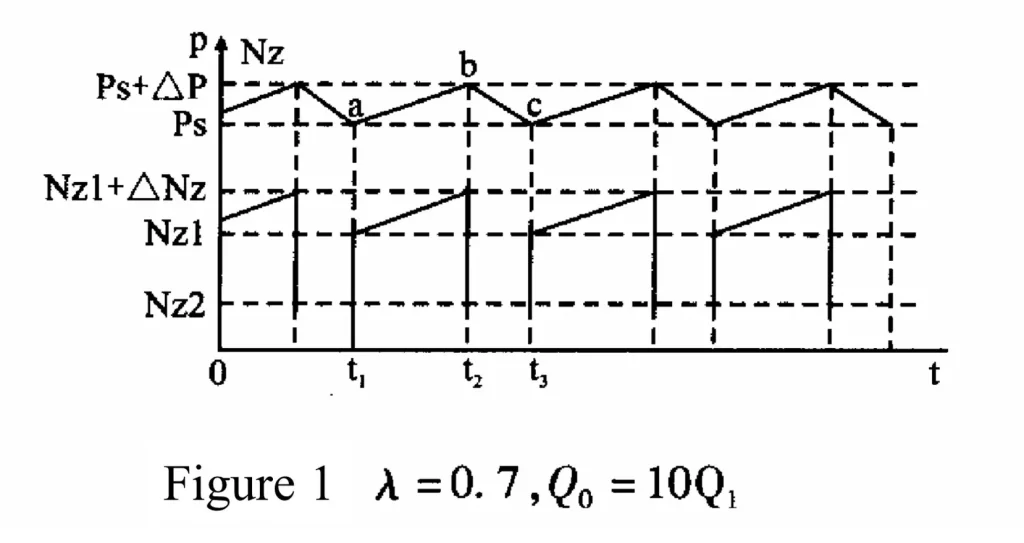
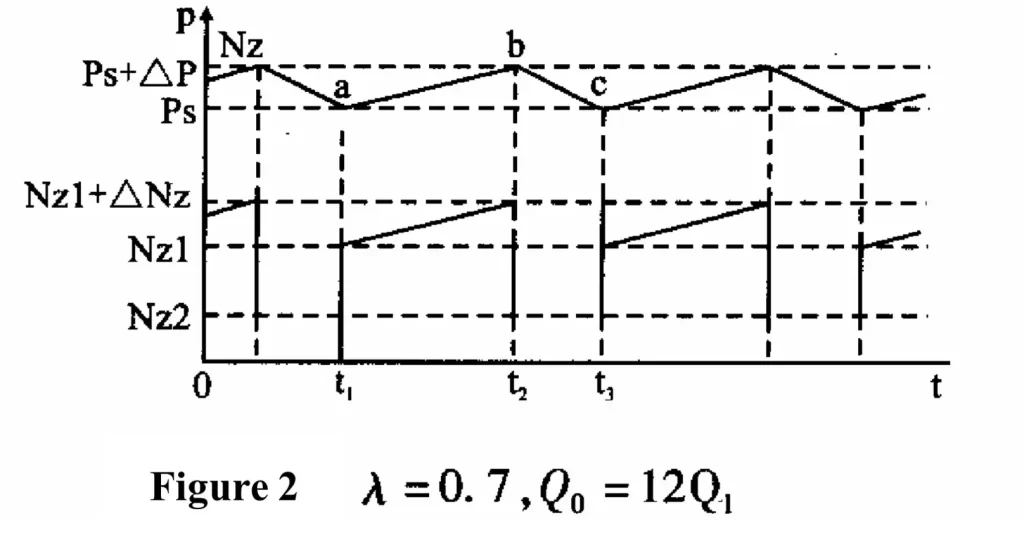
3. Analysis of variable frequency Retrofit of Screw Air Compressor operation
We know that the relationship between the speed of an AC asynchronous motor and the frequency of the power supply follows this relationship:
n = 60×f/p×(1-s)
Where f is the frequency of the power supply, f is the frequency of the motor winding, and P is the number of pole pairs of the motor winding.
For an AC asynchronous motor, p is a fixed value, s is basically unchanged, so n and f constitute a linear relationship, changing the frequency of the power supply f can change the speed of the motor. The exhaust volume of screw compressor is directly proportional to the rotational speed, so we can get this relationship:
Qf = Qe×nf / ne
Where Qf is the exhaust volume under the state of frequency conversion, Qe is the exhaust volume under the state of rated frequency, nf is rotational speed in frequency conversion state, ne is the rotation speed under the rated frequency condition.
It can be seen that by changing the frequency of the power supply, the running speed of the main motor of the compressor can be changed, which in turn changes the exhaust volume of the compressor. Inverter screw air compressor is based on this principle. The so-called variable frequency screw air compressor is by adjusting the compressor main motor frequency to realize the screw air compressor exhaust volume change.
At present, most of the operating frequency of inverter screw compressor is automatically adjusted by the frequency converter according to the difference between the desired pressure set by the user and the real-time pressure feedback from the gas supply side. When the feedback real-time pressure of the gas supply side exceeds the desired pressure set by the user, the frequency converter reduces the output frequency, and when the feedback real-time pressure of the gas supply side is equal to the desired pressure set by the user, the frequency converter maintains the real-time output frequency. Figure 3 gives a trend diagram of the relationship between the supply pressure of the inverter screw compressor and the inverter output frequency when λ=0.7 and Q0=10Q1. As can be seen from Figure 3, for the inverter screw air compressor, unless its gas supply is absolutely unchanged, its operation process is a dynamic equilibrium process, which is the output frequency of the system between the upper limit and the lower limit of the frequency constantly changing to seek the balance of gas supply and demand process.
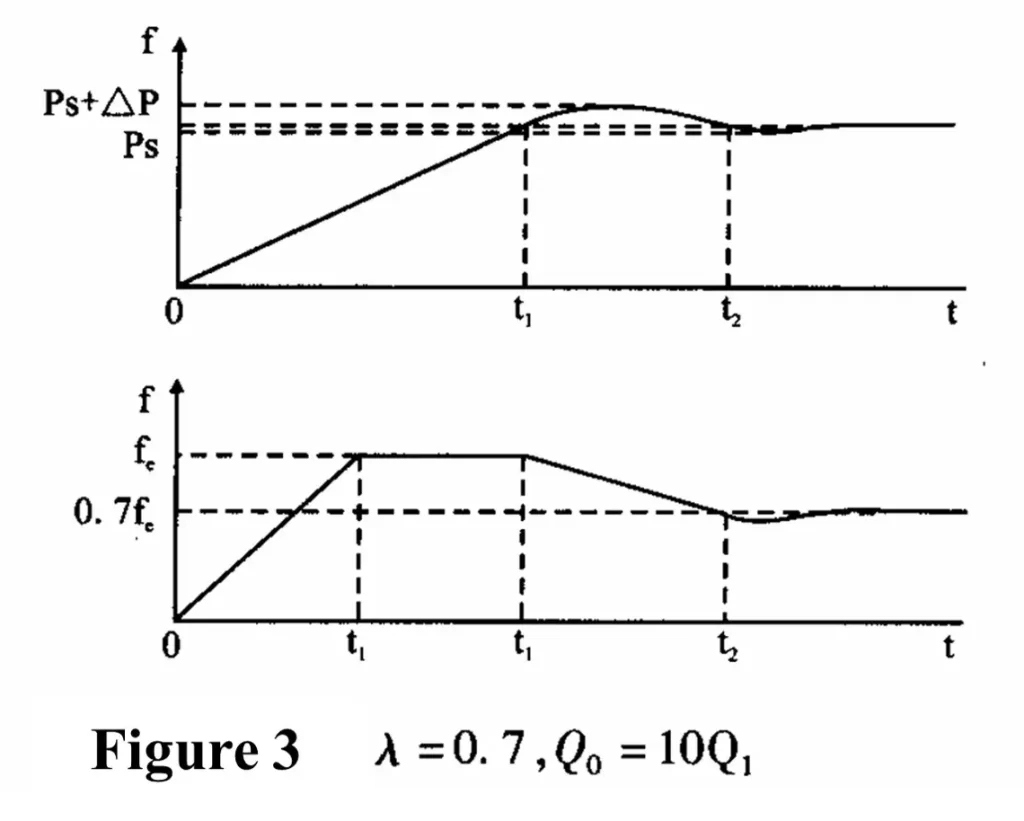
4. Economic analysis of frequency conversion
After the common screw air compressor is transformed by frequency conversion, the main motor speed is determined according to the supply pressure needed for production, and the fan motor speed is determined according to the requirement of exhaust temperature, so as to achieve the purpose of energy saving. In addition, the air compressor stops idling, thus eliminating no-load loss. From the actual transformation of the results, after the transformation of the average power saving rate can reach 15% to 25%. One-time investment in equipment can usually be one year to one and a half years of operation in the full recovery. At the same time, the frequency conversion also brings other benefits.
- (1) Stable exhaust pressure, exhaust temperature is basically a constant temperature, the quality of the gas source is greatly improved.
- (2) The compressor oil life is greatly improved, reducing the number of oil changes.
- (3) Air compressor inlet valve opening and closing times are greatly reduced, its life significantly improved.
- (4) The motor realizes soft start, eliminating the electrical and mechanical shock, the service life of the compressor and the maintenance cycle will be greatly extended.
- (5) In most cases, the operating noise of the unit is significantly reduced.
5. Technical program for frequency conversion: Retrofit of Screw Air Compressor
5.1 Determination of the upper and lower limit frequencies of the frequency converter
We should learn to determine the output frequency range of frequency conversion screw air compressor, from our test data, when the frequency is lower than the rated frequency of 30%, the efficiency of the system decreased significantly. And then from the motor operating characteristics, due to the compressor’s constant torque characteristics, when the motor in the rated frequency of 30% below the operation , its operating current will remain in the rated current near, or even greater, and because of the ordinary asynchronous motor cooling method are self-cooling, so in the rated frequency of 30% below the long-term operation of the state, the motor’s heat dissipation is a problem that can not be ignored. Combined compressor and motor factors, we believe that: 75kW below the frequency conversion screw air compressor output frequency adjustment range in the rated frequency between 30% and 100% is more reasonable; 75kW and above the frequency conversion screw air compressor output frequency adjustment range in the rated frequency between 40% and 100% is more reasonable.
5.2 Inverter modification of the cooling system which should not be neglected
After frequency conversion of ordinary screw compressors, most of the cases run at rated frequency below, when the gas production is lower than the rated gas, the heat load generated is less than the rated frequency operating state heat load, if you still use the fixed-speed fan cooling, the compressor oil will be overcooled by the condensate produced by the emulsification of the oil. Therefore, ordinary screw compressor frequency conversion should be comprehensive consideration of the cooling system into the frequency conversion. In addition, from the point of view of energy saving, the cooling system for frequency conversion of its energy-saving effect is more obvious. Usually, the screw compressor fan or pump system for frequency conversion, on average, can receive more than 30% of the energy saving effect.
5.3 Specific control points of frequency conversion transformation
Ordinary Retrofit of Screw Air Compressor frequency conversion can be considered from the following aspects.
- (1) in the choice of frequency converter, you should give priority to vector type or direct torque control frequency converter, which is mainly determined by the compressor’s torque characteristics.
- (2) for air-cooled common screw compressor transformation, the cooling fan inverter can choose V / F type inverter, and temperature transmitters constitute a closed-loop control. For water-cooled common screw compressor transformation, you should also consider the adjustment of cooling water.
- (3) Select a strong anti-electromagnetic interference pressure transmitter, with the main inverter to form a closed-loop pressure control.
- (4) If the transformation budget allows, the system should be configured with PLC and human-machine interface, in order to improve the intelligent operation and management of the system.
6. Conclusion
Compressors, fans and pumps and other fluid equipment using frequency control technology to achieve energy-saving operation is a key technology to promote energy conservation and emission reduction. Practice has proved that frequency conversion technology for compressors, fans and pumps and other fluid equipment, not only to improve the efficiency and reduce energy consumption, but also improve the level of production technology, and therefore greatly reducing the maintenance of equipment, and repair costs, direct and indirect economic benefits are very obvious.