Discussion of Safety Retrofit Technical Solutions for Screw Air Compressors
2024-04-03
The main pressurized fan for mining is the main equipment of the pressurized air system of the mine, which provides air power for production and supplies air for the pressurized air self-rescue system of the gas protruding mine, which is an important guarantee for production and safety. Mines should set up air compressor stations centrally on the ground; when air compression equipment is set up underground, screw air compressors should be used. In actual work of most coal production enterprises, the energy consumption of compressed air accounts for 10% to 30% of the total power consumption. Compared with electric heating equipment, the waste heat recovery of air compressors requires almost no energy consumption and is a clean and environmentally friendly way to save energy. For the waste heat recovery of mining air compressors, scholars have carried out relevant research, air compressors in the utilization of waste heat recovery technology in coal mines has the operability and feasibility and meet the conditions of economic and safety. For a mine with the vertical extension of underground mining and coal mining will be put into, the original three sets of air compressors will not be able to meet the underground work of the air supply, in order to meet the subsequent mining, we have purchased two sets of air compressors (four with a standby) to meet the needs of the subsequent production. Now we want to set up a set of waste heat utilization system of air compressor to achieve the purpose of energy saving and emission reduction, under the premise of ensuring the safety of installation and renovation, in order to maximize the recovery of this part of the waste heat as far as possible to reuse, through the calculation and analysis of the recovery system of the recoverable power, the power can be utilized, we should study the use of recovered power methods and ways to explore ways to improve the safety of the waste heat utilization of the technical solutions.
1. Calculation and analysis of recoverable power
Screw Air compressor is composed of air end, motor, transmission mechanism, cooling system, control system and outer cover and other parts; the working principle is by a pair of parallel meshing screw (male and female rotor) in the air end constantly cyclic operation and produce volume changes, to complete the process of compressed air. Air is compressed under high pressure, the temperature rises suddenly, the screw’s high-speed rotation rubs heat, the heat generated by these, through the cooling lubricant (referred to as circulating oil) to join the mixture of oil, gas discharged from the air end, through the cooler cooling discharged to the atmosphere, which consumes a large part of the total power of the air compressor.
Recoverable power calculation: the motor power of the compressor is W, in the suction, compression to the exhaust of the whole process, the system provides the loss of power (mechanical loss, heat loss, etc.) Ws, isothermal compressed air power Wy, compressed air kinetic power Wd and mixed oil and gas thermal power Wr, establish the relationship between the equation: W = Ws + Wy + Wd + Wr, Wr is the recoverable power of the air compressor.
The isothermal compressed air power Wy calculation of air compressor: the basic parameters are provided by the nameplate of the equipment, with working pressure Pa (MPa), volumetric flow rate Q (m³/min), standard atmospheric pressure P0 (MPa), and the volumetric flow rate is converted into Q ′ (m³ / s), then the isothermal compressed air requires a minimum of power Wymin = 0.278 × Pa × Q ′ × Ln (Pa / P0), of which, 1MJ/s = 0.278kW.
Compressed air kinetic power Wd calculation: standard atmospheric pressure air density ρ, converted to standard atmospheric pressure under the volumetric flow Q0 = (Pa × Q′) / P0, the mass of compressed air remains unchanged, standard atmospheric pressure before compression of air mass is m0 = m = ρ × Q0, the exhaust port pipe diameter φ, the cross-sectional area of the mouth of the pipe is S, the exhaust port of the gas velocity u = Q′ / S, then the minimum compressed air kinetic power Wdmin = 0.5 × m × u².
Air compressor system loss power W, including mechanical friction loss and thermal energy dissipated due to compression of gas, adiabatic efficiency of air compressor ηd is only 75% to 90%, the efficiency of high-performance motors can reach more than 92%, where Ws is approximately equal to the motor loss and dissipation of thermal energy and, then, the loss of the system of power Ws = W × (1 – η) + W × (1 – ηd), η takes 0.92, ηd takes 0.88.
The recoverable power Wr of the air compressor is calculated: Wr = W-Ws-Wy-Wd, and the calculated data is shown in Table 1.
Table 1 shows that an air compressor can recover waste heat power Wr = 168.846KW, accounting for 67.5% of the total power, and the recoverable waste heat power of 4 sets of operation reaches 675.384kW, which is a large space for recycling.
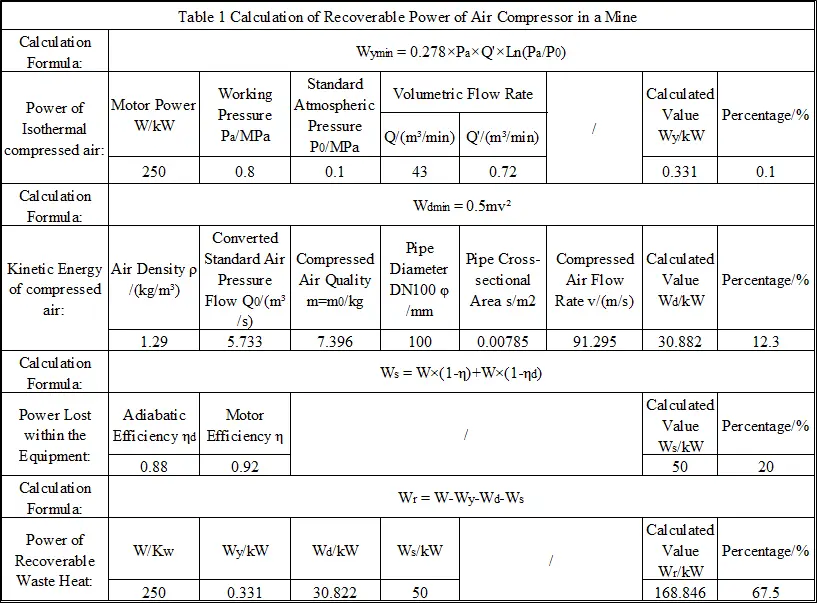
2. Calculation and analysis of available power
The main Screw Air compressor is one of the main equipments in the mine, and the added waste heat recovery system replaces the cooling system of the original air compressor, so the renovation must ensure that the original air compressor meets the following three requirements: firstly, to ensure that it does not destroy the normal work of the air compressor, secondly, to ensure the normal oil temperature, and thirdly, to ensure that the system is safe, reliable and stable in operation.
The recoverable power of the compressor is taken away by the compressed air and circulating oil, because the specific heat capacity of circulating oil in liquid phase is larger than that of the air, the test shows that the circulating oil contains about 75% heat energy and the compressed air contains about 25% heat energy. There are two types of waste heat recovery units in the market, single heat recovery unit that recovers circulating oil heat energy and double heat recovery unit that recovers oil and air heat energy at the same time, 25% of the recoverable power of the mine is 168.846kW, the compressed air contains considerable value of heat recovery, so it is recommended to use double heat recovery unit.
In order to ensure the normal work of the air compressor, according to the requirements of the on-site air compressor instruction manual, the temperature range of the working environment of the equipment: 1.7 ~ 46℃; exhaust temperature shall not exceed 120℃; to ensure the mobility of the circulating oil, the oil temperature is about 70 ℃. Mine air compressor unit operation is shown in Table 2, to improve the available power, the oil temperature after recycling is close to 70 ℃, the exhaust temperature is close to the ambient temperature, when the available power is the largest, the following calculation of a single compressed air can be used to power W’.
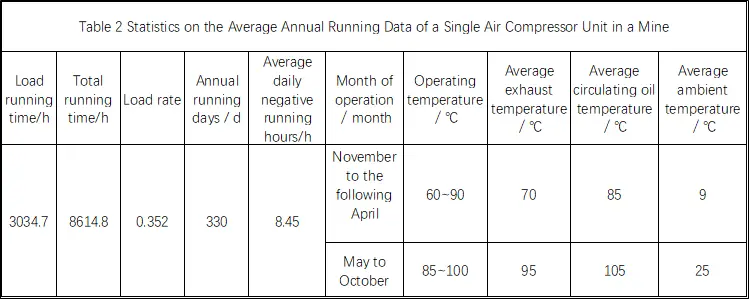
Compressed air providing recycling system power Wq calculation: As the volume flow of compressed air in the inherent parameters of the equipment is 43.0m³ / min, so the temperature rise Δt (℃) determines the power that can be provided to the recycling system, the results of the calculations are shown in Table 3. November to the following April accounted for 14.8% of the recoverable power, May to October accounted for 16.9%, take 15% to calculate, Wq = 25.327kW. The compressed air will still take away 10% of the recoverable power.
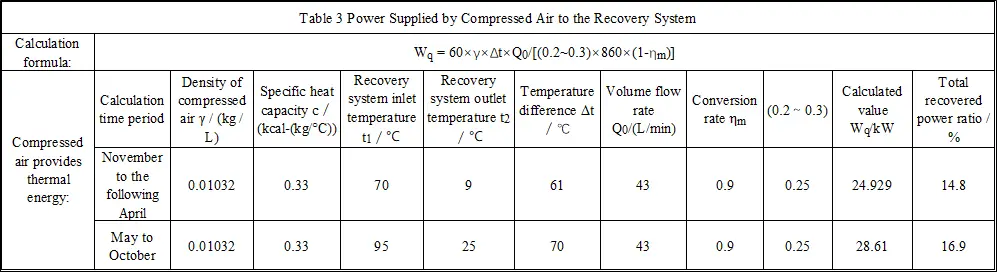
Circulating oil providing recycling system power Wl calculation: Wl is determined jointly by the volume flow rate of the recycling oil Ql and the temperature difference Δt, the volume flow rate of Ql is inversely proportional to the difference in temperature Δt, and a too large flow rate will cause the outlet oil temperature to be less than 70°C, and a too small flow rate will result in a low recovery rate of the recycling system. In order to ensure the normal operation of the compressor, the power Wl of the recovery system is maximum and stable, the recovery system has a circulating oil flow adjustment device that changes with the temperature difference Δt, and the adjustment range is 1.601-3.735L/min, which can maximize the power of the recovery system.
To sum up, when the circulating oil is adjusted with the temperature difference within the above range, it can be guaranteed that a single air compressor can provide the maximum utilizable power W′max = 151.961kW, which accounts for 60.8% of the total power, and then 4 air compressors can provide 607.844kW. Assuming that the efficiency of the recycling unit provided by the manufacturer can reach more than 90%, and calculating with 90%, the converted and utilizable power of the recycling system will be 547.060kW.
(6) High-temperature shutdown failure. Generally speaking, there are four main reasons for high-temperature shutdown failure, one is a poor electrical connection, you can check whether the contact of the air compressor motor is intact; the second is the high temperature of the working environment, you can ventilate the process to reduce the ambient temperature; the third is the insufficient circulation of the cooling oil, you can check whether there are impurities in the cooling oil, the quality of whether the standard; the fourth is the effect of the cooling is not good, you can check the cooling system is not a problem.
3. Utilization of recovered power
The recovered power of the recovery system is generally used for heating and bathing, combined with the actual mine, there are four places where the recovered power can be utilized, because of the intermittent work of the air compressor, resulting in unstable heating, so the recovered power can not be used to supply heat alone, and needs to be used in conjunction with other heat supply systems to produce heat together.
Because the heat recovery system replaces the cooling system of the original compressor, in order to ensure the safe operation of the compressor, the recovery system must be synchronized with the operation of the compressor, that is, to ensure that the compressor operates 330d throughout the year, the recovery system can operate normally, so as to achieve the purpose of heat dissipation for the compressor. And in docking with other heating systems we must ensure that the original system’s heat supply is stable.
The configuration of air source heat pump unit for shower in the joint building of the mine works 15h per day from May to October; the unit in the air heating room supplies heat for the main and secondary inclined shafts, and it works 16h per day from November to April. If the DN200 pipe line is used for direct buried single pipeline to supply heat, and if the heat loss of each pipeline conveying 1m is calculated to be 0.1kW, we can get the result that the recycling system not only ensures stable operation of the compressor but also ensures waste heat utilization all the year round.
4. Conclusion
In the process of generating compressed by air compressor, 100% of the shaft power is converted into heat, and more than 90% of the heat energy is wasted. Recycling this heat not only improves the efficiency of the compressor, but also improves the service life of the compressor. Screw air compressors, with their own structure and function, have a great potential for waste heat recovery, with obvious economic benefits. In order to find a secure solution for the efficient enhancement of heat waste utilization of screw air compressors suitable for mine production, the efficiency and productivity of air compressors can be improved, so as to achieve the purpose of energy saving and emission reduction. By testing a set of screw air compressors that a mine wants to put into use, calculate the recoverable power and utilizable power of the waste heat utilization system, and analyze the benefits of the above indexes, and conduct different pilot studies on the methods and ways of utilizing the recovered power, we finally get the technical solution for improving the heat residual utilization of the screw air compressors in mines and the safety renovation:
(1) Ensure that the normal work of the air compressor is not damaged, that is, not to damage the air compressor’s transmission mechanism, control system, heat dissipation effect, etc. so that the air compressor can not be operated normally; ensure the normal oil temperature of the air compressor; ensure that the recycling system, the docked heating system is reliable and stable, and that the amount of heat supplied by the recycling system meets the requirements.
(2) Adopt double heat recovery unit which recovers oil and gas heat energy at the same time, and the power of waste heat utilization can be increased by 15%.
(3) Adopt the recycling system with temperature difference Δt changes in the circulating oil flow regulation device, which can improve the waste heat utilization power of the circulating oil.
(4) Select the heat supply place reasonably and shorten the distance of recycling power transportation. Read more