1. What is piston air compressor?
The piston air compressor is the most common type of volumetric compressor, which consists of a crank linkage mechanism that changes the rotary motion of the driver into the reciprocating motion of the piston. The working chamber of a piston compressor consists of a piston and a cylinder. Relying on the reciprocating motion of the piston in the cylinder, and with the help of the automatic opening and closing of the inlet and exhaust valves, it enables the gas to periodically enter the cylinder working chamber for compression and discharge.
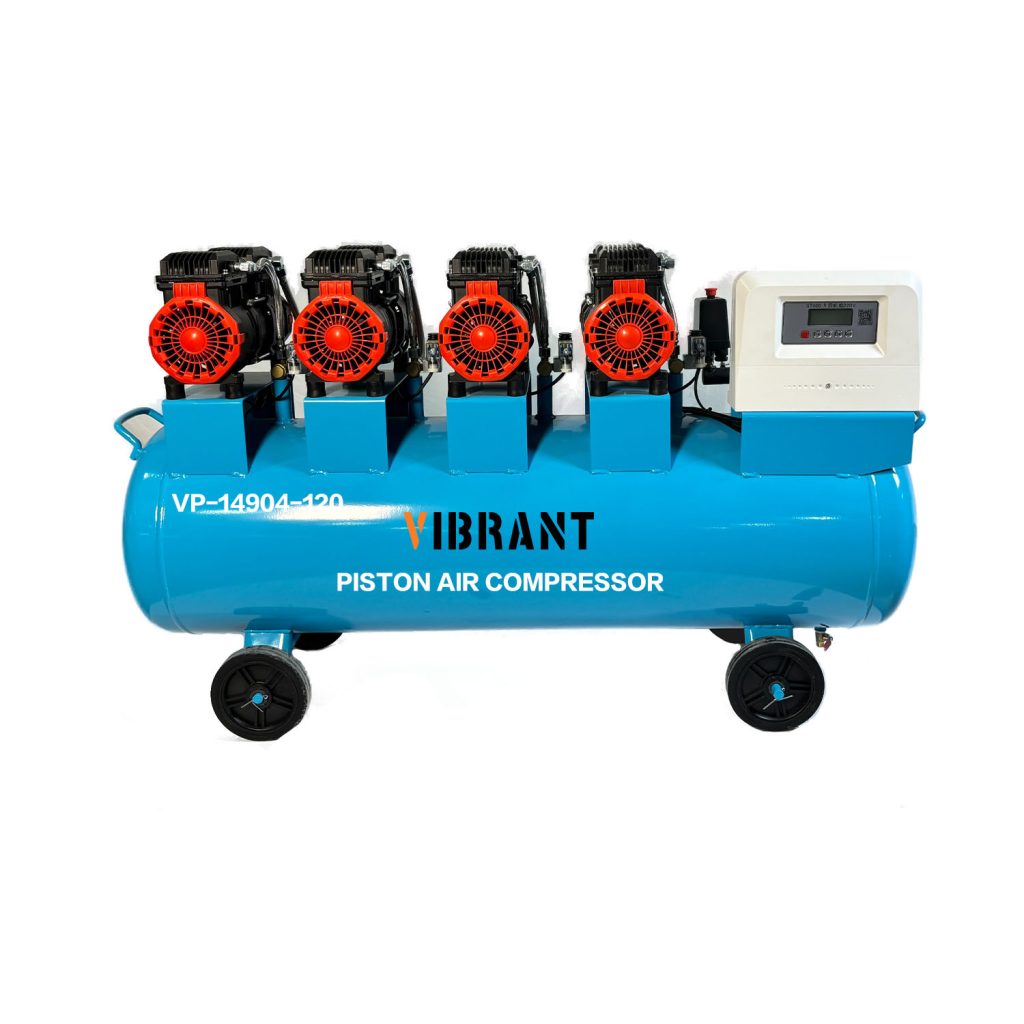
Piston compressor is mainly composed of three main parts: the moving mechanism (crankshaft, bearings, connecting rods, crossheads, pulleys, or couplings, etc.), the working mechanism (cylinders, pistons, valves, etc.) and the body. In addition, there are three auxiliary systems: lubrication system, cooling system and regulation system.
The moving mechanism is a crank linkage mechanism that changes the rotary motion of the crankshaft into the reciprocating motion of the crosshead. The body is used to support and install the whole moving mechanism and working mechanism. The working mechanism is the main component to realize the working principle of the compressor.
2. How does a piston compressor work?
In the pneumatic drive, the volume type piston air compressor is usually used. Piston air compressors utilize the reciprocating motion of the piston driven by the crankshaft to compress the gas in the cylinder chamber and produce compressed air continuously. Piston air compressor belongs to volumetric compressor, the working principle and characteristics of this model are limited, piston air compressor is equipped with storage tank generally to supply stable air.
3. Why should you get piston compressors?
There are four clear advantages of piston air compressor:
① Wide range of applicable pressure. Because the piston compressor relies on the principle of volume change to work, regardless of its flow size, it can reach a very high working pressure. At present, has been made of low, medium, high, ultra-high pressure compressors, including industrial ultra-high pressure compressor working pressure up to 350MPa (3500kgf/cm2).
② Low equipment price, low initial investment, easy to operate, long service life.
③ The compression process is a closed process, so the thermal efficiency is high.
④ Strong adaptability, wide range of exhaust volume, and less affected by changes in exhaust pressure, when the medium weight changes, the exhaust volume and pressure changes are also small.
4. What are the disadvantages of piston air compressor?
① Large inertial force, the speed cannot be too high, so the machine is more bulky, especially when the discharge volume is large.
② Complex structure, more wearing parts, a large amount of maintenance work, maintenance costs are relatively high.
③ Discharge is not continuous, the airflow pressure will be pulsating, easy to produce air column vibration.
④ During operation, vibration and noise are high, and the requirement of equipment installation foundation is high.
5. Where can piston air compressors be used?
Piston compressor belongs to a reciprocating compressor, the pressure level belongs to the medium pressure, high pressure, ultra-high pressure level, suitable for higher pressure occasions, the flow rate for the medium and small flow range, mainly for small and medium exhaust volume, higher pressure occasions.
6. How will piston compressors evolve?
Piston compressors are traditionally the most widely used compressors in the field, but with the rise of other rotary compressors and other products, their market in many areas, such as refrigeration, is shrinking.
Piston compressors are mainly developed in the direction of large capacity, high pressure, low noise, high efficiency and high reliability; The structural parameters of piston compressors are developed in the direction of high speed, short stroke and compact structure, while extending the life of wearing parts such as valves and sealing elements in order to improve the operation rate; continuously develop new types of valves that operate under variable operating conditions to improve valve life; In product design, the application of thermodynamics, kinetic theory, through a comprehensive simulation, to predict the performance of the compressor in the actual working conditions; enhanced mechatronics of the compressor with calculated automatic control for optimized energy-saving operation and in-line operation.