Screw air compressors (hereinafter referred to as ” air compressor “) are widely used in railroad locomotives, moving trains and subway cars. Oil-lubricated air compressor emerged in the 1970s. After years of practical use, they have shown excellent comprehensive performance.
1. How does an oil-gas separator work?
An air compressor contains a pair of mutually compatible yin and yang rotors. During the rotation of the rotors, the space between the rotors and the casing is continuously compressed, thus raising the gas pressure. The rotor unit is shown in Figure 1. During the operation of the air compressor, lubricant is injected into the inside of the rotor body to seal the contact areas between the rotor and the rotor and between the rotor and the casing, and at the same time absorbs and carries away most of the heat generated by compression. The air compressor is mainly composed of 2 parts: the oil circuit and the air circuit.
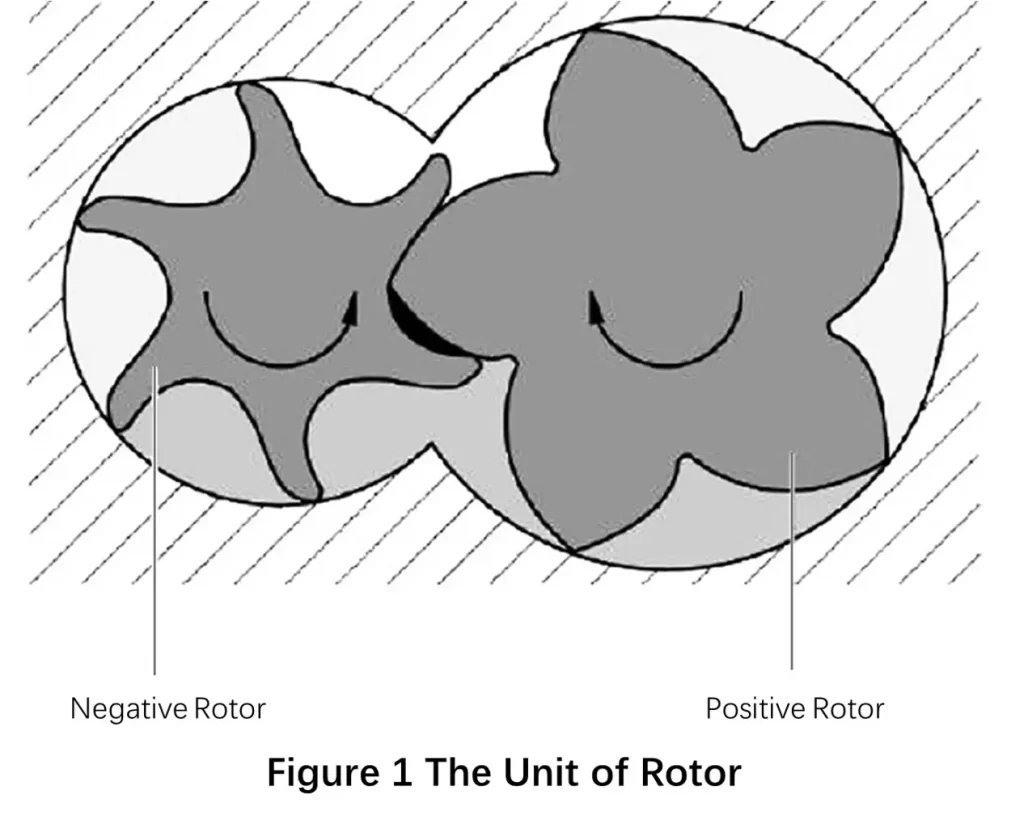
(1) After the external air is filtered by the air filter, it enters the rotor unit, where the pressure rises under the meshing and squeezing of the negative and positive rotors, and mixes with the lubricant inside the rotor to form a high-temperature and high-pressure oil-air mixture, which then enters the interior of the air compressor body through the exhaust pipe. The oil baffle plate is set inside the body, which separates about 80% of the lubricating oil in the compressed air and allows the oil to flow back to the bottom of the body. The compressed air after the initial separation then passes through the oil-air separator to filter out the remaining lubricant and is cooled by the air radiator and discharged through the air outlet.
(2) The lubricating oil is injected into the body of the compressor through the refueling port, and the rotor unit is immersed in the lubricating oil to cool the rotor unit. During the operation of the compressor, the pressure inside the body rises, and the lubricating oil passes through the oil filter and enters the oil control unit under pressure. Part of the lubricating oil enters the rotor unit directly, and the other part enters the rotor unit after cooling through the radiator. Temperature control valve is set inside the oil control unit to regulate the amount of lubricant entering the radiator. The lubricating oil that enters the rotor unit enters the compressor body together with the compressed air and returns to the bottom of the compressor body due to the primary separation by the oil baffle plate. The remaining lubricating oil is filtered through the oil-air separator to the bottom of the oil-air separator. Through the oil return pipe and check valve, the oil enters the rotor unit again.
2. Cause analysis and solution measures
Lubricant plays a very critical role in the normal operation of the air compressor. Generally, the normal exhaust oil content is about 1mg/m³, once the oil content of the exhaust gas is high, there will be a large number of oil traces in the pipeline and components of the compressor, which will also cause rapid consumption of lubricant, rotor wear, and a decrease in the volume of exhaust.
2.1 Excessive refueling in daily maintenance
The refueling volume of the air compressor is strictly controlled, and the refueling volume and oil level will be checked at the factory. But in the actual use and maintenance process, often in the refueling process, the refueling volume is too much. When the oil level is high enough to be close to the position of the oil baffle plate, the primary oil filtration function assumed by the oil baffle plate will be reduced or even invalidated. Most of the lubricant mixed in the compressed air will be blown to the oil-air separator with the compressed air, resulting in an excessive burden on the oil-air separator. Under this environment operation for a certain period of time, the performance of the oil-air separator will be reduced and its service life will be shortened. When the performance of the oil-air separator decreases or fails, the function of oil-air separation is significantly affected, and the lubricating oil will be transported with the compressed air to the subsequent pipeline. Therefore, in the daily maintenance you should strictly follow the instructions to control the amount of lubricant refueling. When the refueling amount is too much, the excessive lubricant should be discharged through the oil drain valve in time, the contaminated oil-air separator should be replaced, and the minimum pressure valve, radiator and subsequent pipelines should be cleaned.
2.2 Oil-gas separator not replaced on schedule
Oil-gas separator is a kind of filtration parts, and it is also a fragile and consumable part. Under normal circumstances, the air compressor must be replaced with a new oil-air separator every 3000h of operation or 2 years (whichever comes first). In high temperature, wind and sand and other extreme weather, the replacement cycle is shortened accordingly. If the oil-air separator is not renewed in time, the performance of the old oil-air separator will be greatly reduced or even fail, resulting in high oil consumption and faults of the air compressor.
When the oil-air separator is not replaced on schedule and the exhaust gas has high oil content, the failed oil-air separator should be replaced in time, the replacement time should be recorded and the replacement cycle should be adjusted. At the same time, replace the lubricating oil and clean the minimum pressure valve, radiator and subsequent pipelines.
2.3 High oil temperature of air compressor
During normal operation, the temperature of the air compressor body should be 80℃~90℃. When there is a temperature control valve fault, the body of the internal lubricating oil content is low, it will cause high temperature inside the body of the air compressor. If the oil-air separator operates in this environment for a long time, its performance and service life will be greatly shortened. When the oil-air separator performance drops or fails, a large amount of lubricating oil accompanies the compressed air and is transported to the subsequent pipeline. In this way, due to high oil temperature when the air compressor is running there is a possibility of temperature switch disconnection protection.
When the high oil temperature of the air compressor leads to high oil content in the exhaust air, the lubricant oil level should be checked in time. If the lubricating oil is insufficient, the lubricating oil should be replenished. Check whether the temperature control valve opens and closes normally, if it can not open normally, it is necessary to replace the temperature control valve and the contaminated oil-air separator in time. Also clean the minimum pressure valve, radiator and subsequent piping.
2.4 Clogged oil return pipe
The lubricating oil separated by the oil-air separator returns to the rotor unit through the oil return pipe. The return pipe is equipped with a filter screen, with an aperture of about 1.5mm, which can filter out the impurities in the lubricant and prevent them from entering the rotor unit with the lubricant and damaging the rotor. When the lubricating oil contains a lot of impurities, the filter screen of the oil return pipe is very easy to be clogged, and the lubricating oil filtered by the oil-air separator will not be able to return to the inside of the rotor unit through the oil return pipe. The lubricant will accumulate inside the oil-air separator, contaminating the oil-air separator and being transported with the compressed air to the subsequent lines. When there is a clogged return line, the lubricating oil, return line and contaminated oil-air separator should be replaced in time, and the minimum pressure valve, radiator and subsequent piping should be cleaned.
2.5 Poor sealing of suction outlet check valve plate
The check valve is a one-way valve, in the shutdown state, the check valve is closed, while the valve plate plays a sealing role to prevent the high-pressure oil and gas mixtures inside the body blowing back into the air filter. When the check valve plate is not sealed properly, the lubricating oil inside the body will be blown into the air filter during the shutdown. During routine maintenance and replacement of the air filter, a large amount of oil was found in the suction port. This will cause the lubricating oil content inside the air compressor body to decrease, the lubrication and cooling effect will be reduced, and the rotor and oil-air separator will be damaged, which will cause the lubricating oil not to be separated effectively, and the oil content of the exhaust air will be high.
When the exhaust oil content is high due to poor sealing of the suction port check valve plate, the pressure relief valve body and valve plate and air filter should be replaced in time. At the same time, replace the contaminated oil-air separator, clean the minimum pressure valve, radiator and subsequent piping.
2.6 Using unsuitable lubricating oil
The lubricant of the screw air compressor has strict regulations, only in accordance with the lubricant specified in the instruction manual for maintenance, in order to ensure the normal operation of the air compressor. Unsuitable lubricant will have chemical reaction with the metal material or protective coating in the body, polluting the lubricant and producing impurities. Long-term accumulation will block the radiator, oil return pipe. Unsuitable lubricant is also very easy to emulsification, loss of lubrication function, damage to the machine.
If the use of unsuitable lubricating oil leads to faults, the lubricating oil should be drained in time and the specified lubricating oil should be used to repeatedly flush the inside of the machine body, replace the contaminated oil-air separator, and clean the minimum pressure valves, radiators, and subsequent piping. Retest to check machine performance.
3. Conclusion
Air compressors are widely used in China’s railroad industry, and the phenomenon of high oil content in exhaust gas is widespread. The reasons for the high oil content in the exhaust of the air compressor vary greatly. Therefore, we need to analyze the reasons for high exhaust oil content, and put forward corresponding measures to solve the problem, which has a certain guiding role in the use of air compressors, maintenance and troubleshooting.