PM Air Compressor
Air compressors that can help companies solve their problems.
Permanent Magnet Frequency Conversion Screw Air Compressor
Permanent Magnet Frequency Conversion Screw Air Compressor, which also called PM VSD screw air compressor, is a type of screw air compressor that employs permanent magnet synchronous motor (PMSM) and frequency conversion speed control technology. This compressor is designed to incorporate the high efficiency of the PMSM and the
energy-saving features of the frequency converter to achieve a better balance between power consumption and power output.
JX-150APMX
- Pressure(MPa): 0.8~1.3
- Exhaust Volume(m³/min): 19.8~14.5
- Power(KW/HP): 110/150
- Dimension(mm): 2550*1680*1900
- Noise dB(A): ≤82±2
- Weigt(kg): 2680
- Pipe Diameter: DN80
- Startup Mode: Frequency Conversion Start
- Power Supply: 380V/50HZ, available for customization(110V~480V,50HZ/60HZ)
-
Energy-efficient
-
Stable operation
-
Low noise
-
Intelligent
Get a quote now
Similar Products
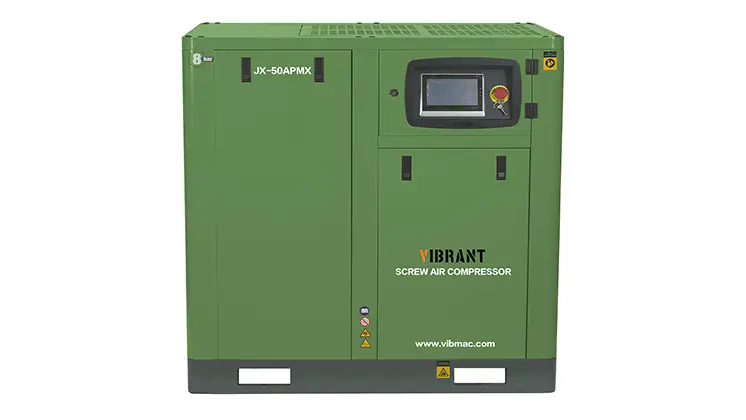
JX-50APMX-37KW
-
Pressure(MPa): 0.8~1.3
-
Exhaust Volume(m³/min): 6.1~4.6
-
Power(KW/HP): 37/50
-
Dimension(mm): 1250*950*1290
-
Noise dB(A): ≤66±2
-
Weigt(kg): 438
-
Pipe Diameter: G1 1/2
-
Startup Mode: Frequency Conversion Start
-
Power Supply: 380V/50HZ, available for customization(110V~480V,50HZ/60HZ)
VIEW MORE
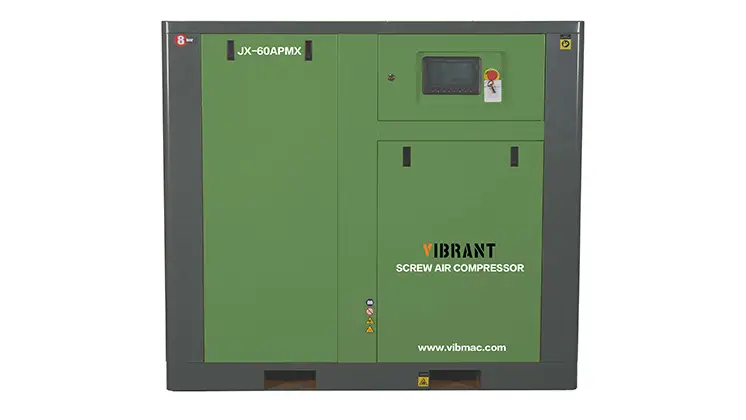
JX-60APMX-45KW
-
Pressure(MPa): 0.8~1.3
-
Exhaust Volume(m³/min): 7.4~5.7
-
Power(KW/HP): 45/60
-
Dimension(mm): 1250*1000*1370
-
Noise dB(A): ≤68±2
-
Weigt(kg): 486
-
Pipe Diameter: G1 1/2
-
Startup Mode: Frequency Conversion Start
-
Power Supply: 380V/50HZ, available for customization(110V~480V,50HZ/60HZ)
VIEW MORE
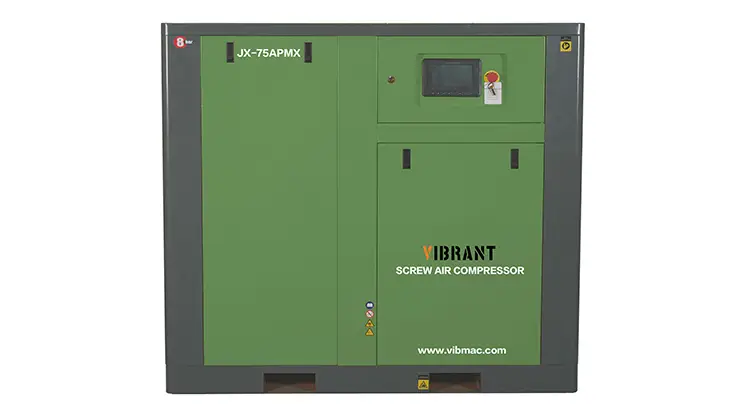
JX-75APMX-55KW
-
Pressure(MPa): 0.8~1.3
-
Exhaust Volume(m³/min): 9.5~6.8
-
Power(KW/HP): 55/75
-
Dimension(mm): 1600*1140*1530
-
Noise dB(A): ≤70±2
-
Weigt(kg): 998
-
Pipe Diameter: G2
-
Startup Mode: Frequency Conversion Start
-
Power Supply: 380V/50HZ, available for customization(110V~480V,50HZ/60HZ)
VIEW MORE
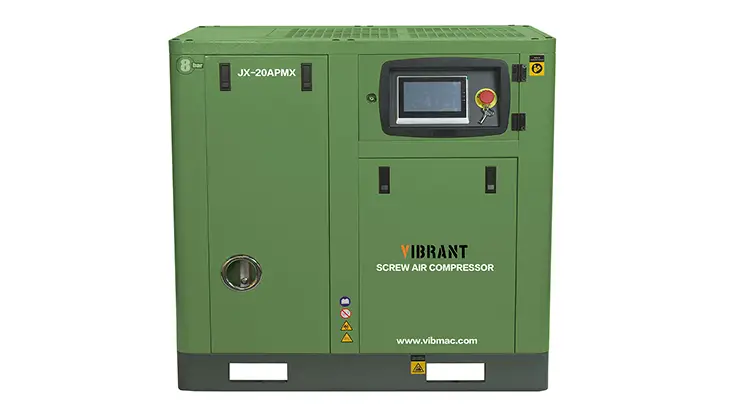
JX-20APMX-15KW
-
Pressure(MPa): 0.8~1.3
-
Exhaust Volume(m³/min): 2.4~1.8
-
Power(KW/HP): 15/20
-
Dimension(mm): 1050*750*1060
-
Noise dB(A): ≤65±2
-
Weigt(kg): 207
-
Pipe Diameter: G3/4
-
Startup Mode: Frequency Conversion Start
-
Power Supply: 380V/50HZ, available for customization(110V~480V,50HZ/60HZ)
VIEW MORE
You May Also Like
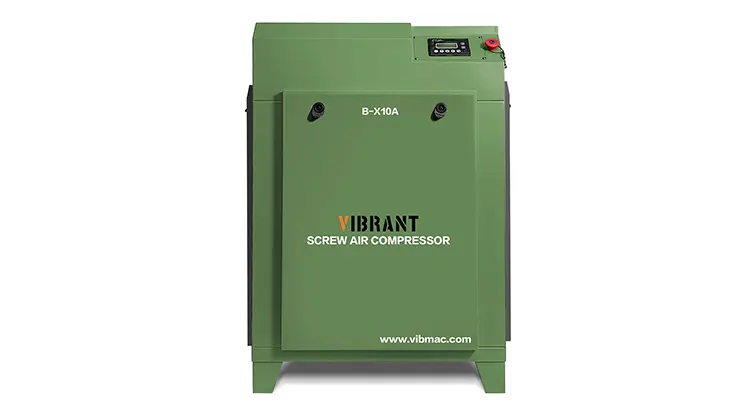
B-X10A
-
Pressure(MPa): 0.8
-
Exhaust Volume(m³/min): 1.1
-
Power(KW/HP): 7.5/10
VIEW MORE
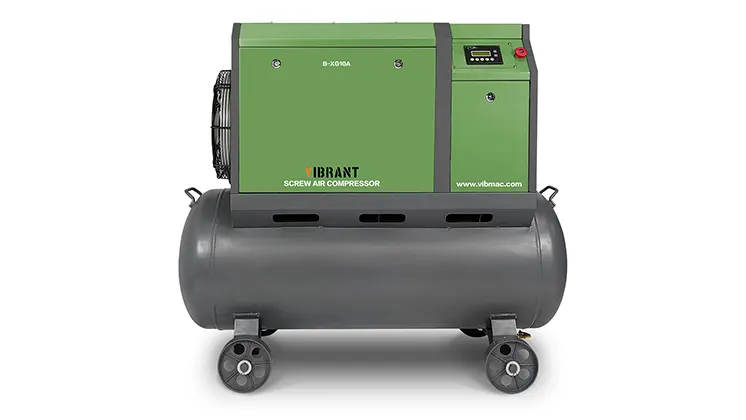
B-XG10A
-
Pressure(MPa): 1.2-1.5
-
Exhaust Volume(m³/min): 0.7-0.63
-
Power(KW/HP): 7.5/10
VIEW MORE
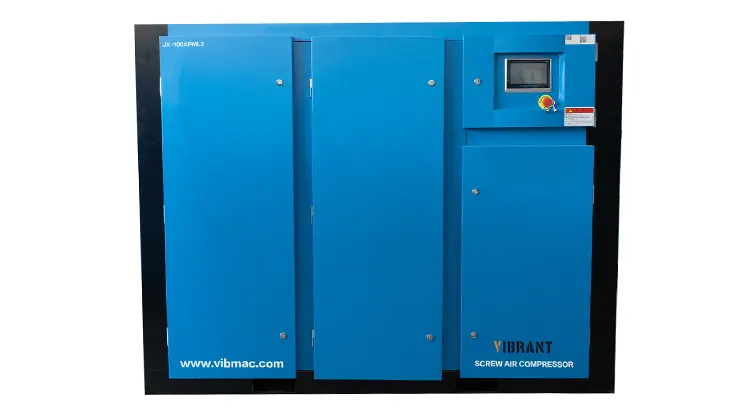
JX-100APML2
-
Pressure(MPa): 1.6
-
FAD (m³/min): 9.0
-
Power(KW/HP): 75/100
VIEW MORE
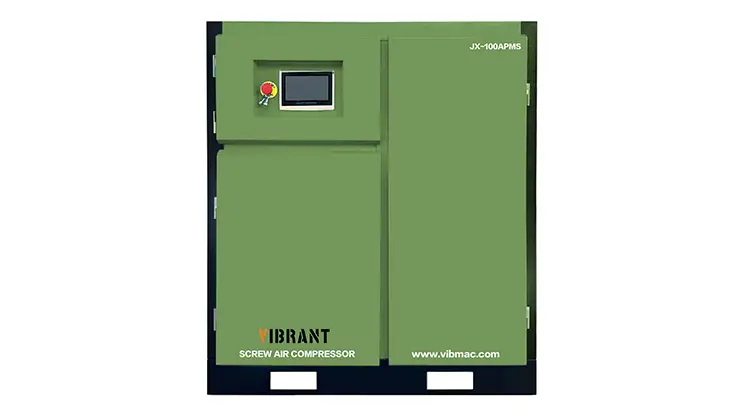
JX-100APMS-100HP/75KW
-
Pressure(MPa): 0.8
-
Exhaust Volume(m³/min): 12.3
-
Power(KW/HP): 75/100
VIEW MORE
Get In Touch